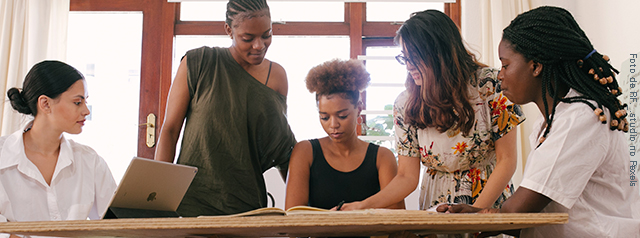
Este artigo tem como objetivo descrever a importância da Cadeia de Ajuda no processo de estabilização produtiva e apresentar métodos de reação aos problemas de instabilidade que aparecem durante a produção.
1. DEFINIÇÃO
A Cadeia de Ajuda é uma rotina de interação e envolvimento entre as pessoas para se resolver um problema quando ele surge, iniciando-se pelo operador da produção e que envolve as lideranças imediatas e os responsáveis de todas as áreas de apoio, eliminando as instabilidades do processo.
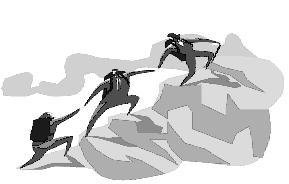
Figura 1: A Cadeia de Ajuda
Também exige das pessoas a tolerância “zero” aos problemas que geram desperdícios, num ambiente onde não é “quem é o responsável” e sim “qual é o problema”. Esse “modelo mental” que predomina na Toyota é um dos responsáveis pela identificação dessas perdas, onde o objetivo não é esconder e sim haver uma sistemática de identificação e resolução, pois os problemas são considerados oportunidades de ganhos.
A Cadeia de ajuda é fundamental no processo de estabilização, conforme descrito no artigo “Estabilidade na Produção na Toyota do Brasil” (ver item 4, “Métodos para garantir a estabilidade”, estabilidade na produção da toyota do brasil).
2. A SEQÜÊNCIA TÍPICA DE AÇÕES
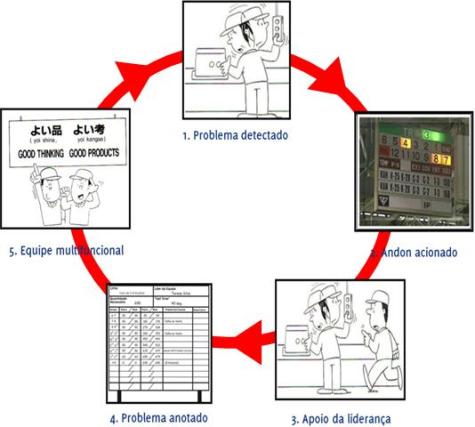
Figura 2: Seqüência de Acionamento da Cadeia de Ajuda
O primeiro acontecimento de uma Cadeia de Ajuda é detectar o problema na sua fonte. Normalmente são problemas de qualidade, quebras ou setups de máquinas, segurança e ergonomia, absenteísmos, ou atrasos dos funcionários. No exemplo acima (ver Figura 2) mostramos o que basicamente deve acontecer.
A primeira intervenção é feita pelo operador, e quanto mais capacitado e treinado ele for mais rápido evitamos as complicações conseqüentes. Mais adiante veremos a importância dessa capacitação (matriz de versatilidade).
O segundo acontecimento depois que um problema ocorre é a maneira como sinalizamos isso, e normalmente utilizamos um sinal luminoso ou sonoro, que é chamado de “Andon” (ver descritivo do artigo Como operar um andon) para alertar à todos os envolvidos. Importante ressaltar que o sinal é dado antes que a produção realmente pare e nesse intervalo o operador e seu apoio devem agir.
O terceiro acontecimento é a assistência do Líder da área após o sinal que indica a existência de problema, de maneira automática e dentro do “Pitch” (um múltiplo do Takt). O operador e esse Líder devem resolver utilizando métodos bem definidos tais como os “5 Por quês” ou o Gráfico de Ishikawa.
O quarto acontecimento surge ao se anotar o problema no quadro de acompanhamento da produção, e a partir dele tomarmos algumas atitudes: se o problema não foi resolvido, a produção é paralisada e acontece o apoio de supervisores, gerentes e responsáveis de áreas pertinentes (grupo multi-departamental). Se o problema foi resolvido ou uma contenção foi feita para não parar a produção, o mesmo é anotado no quadro e segue-se então à sistemática da resolução. Podemos expor os documentos A3 (PDCA), os formulários com as tratativas dos “5 Por quês” e os Gráficos de Ishikawa ao lado do quadro, como uma maneira de dar um retorno aos funcionários da área e os transeuntes.
E o quinto e último acontecimento seria a intervenção do grupo multi-departamental, o qual dará uma tratativa mais adequada com os métodos científicos existentes. Esse grupo multi-departamental é formado por pessoas das mais variadas áreas de apoio, da Qualidade, PCP, Engenharia, Manutenção, Suprimentos, Logística e outros.
Interessou-se pelo tema? Veja o nosso treinamento de Cadeia de ajuda
3. A ESTRUTURA FUNCIONAL E A FREQÜÊNCIA DE APOIO NO GEMBA
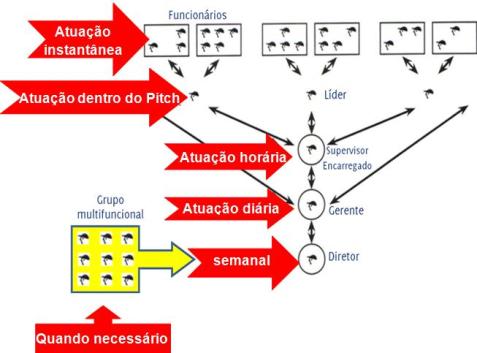
Figura 3: Estrutura Organizacional e Freqüência no Gemba
No organograma da empresa devem existir condições para que esse procedimento de ajuda perante aos problemas ocorra. Exigir das pessoas sem haver condições humanas de trabalho é um problema comum, e que normalmente causa insatisfações e resistências ao procedimento.
Normalmente encontramos a proporção 5:1 no organograma (ver Figura 3), ou seja, um diretor toma conta de cinco gerentes, os quais tomam conta de cinco supervisores ou encarregados, que tomam conta de cinco líderes, e estes de cinco funcionários. OLíder seria aquele funcionário multi-funcional, que pode ser treinado para atuar em outra área, e na ausência do outro Líder deve substituí-lo (matriz de versatilidade do Líder seria direcionado para as habilidades deste em trabalhar e liderar outras áreas), e assim sucessivamente para os cargos de Encarregado, Supervisor, Gerentes e Diretores. Essa capacitação garante que a função superior sempre possa atuar no socorro do seu subordinado, e assim garantir a ajuda ao processo como também incentivar o crescimento das pessoas.
Além dessa condição humana, deve haver o hábito de atuação direta no Gemba, e uma freqüência mínima seria o Diretor no mínimo ir semanalmente, o Gerente estar diariamente, o Supervisor e Encarregado estarem com freqüência horária, o Líder obviamente estarem atuantes dentro do “Pitch” (múltiplo do Takt), e os funcionários terem atitudes imediatas perante ao problemas.
A formação de um grupo multi-departamental com conhecimentos técnicos mais específicos também é imprescindível no apoio a estrutura citada. Esses colaboradores devem ter a missão de ajudar, sob coordenação da gerencia, e resolver os problemas que a área produtiva não conseguiu.
4. DEFINIÇÃO DE RESPONSABILIDADES
Para que a Cadeia de Ajuda funcione para diminuir a instabilidade da produção, tornando-se instintiva e um hábito para todos os envolvidos, deve haver uma clara definição de responsabilidades para que não aconteça a ruptura dessa “corrente” ou haverem duplicidade de ações.
Uma espécie de atitudes padronizadas e organizadas para que de maneira otimizada as pessoas se envolvam, seguindo uma seqüência que vai do operador até a direção.
Como dissemos, a primeira ação deve ser realizada pelos funcionários (ver Figura 4) que devem estar aptos para executarem o trabalho, conforme o Trabalho Padronizado solicita, com treinamento em métodos de resolução dos problemas tais como os “5 Por quês” para rapidamente agirem, acionarem o “Andon” informando à todos que um problema está na iminência de acontecer e parar a linha. E se não conseguir resolver o problema, chamar com urgência o Líder.
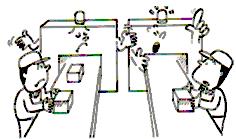
Figura 4: Funcionários treinados conforme o padrão
O Líder (ver Figura 5) começa a sua atuação antes de se iniciar a jornada de trabalho, através de reuniões diárias de 5 minutos, normalmente antes do início de trabalho onde o mesmo observa a presença dos funcionários, e utilizando o Quadro Kanri-ban (Quadro de controle diário da presença e análise da capacitação individual) faz a escala de onde cada um irá trabalhar, observando a matriz de versatilidade. Também é o responsável pela execução do treinamento e capacitação das pessoas, seguindo a matriz de versatilidade determinada pelo supervisor, e analisando as deficiências de pessoas treinadas no quadro Kanri-ban.
Quando as áreas emitem um sinal luminoso-sonoro através do Andon informando a existência de problemas, o Líder deverá se deslocar até a área e auxiliar o funcionário. Agindo de maneira rápida e estando capacitado tecnicamente, deverá analisar dentro do Pitch, além de planejar a solução e executá-la com os recursos existentes. Tem a responsabilidade de identificar os problemas resolvidos ou não através do Quadro de Acompanhamento, pois os casos não solucionados deverão ser tratados pelos superiores.
Uma das atitudes do Líder é a constante observação do Andon, pois o mesmo informa o status da existência de problemas. Quando estiver indicando “verde” a atitude do Líder deve ser preventiva, analisando e planificando melhorias. Quando estiver indicando “amarelo” deverá se deslocar e interagir, e quando estiver “vermelho” deverá agir em conjunto com todos os responsáveis na busca do tratamento da causa.
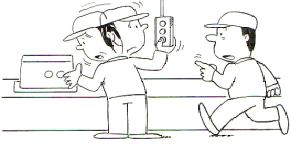
Figura 5: Apoio imediato do Líder
Os Supervisores ou Encarregados (ver Figura 6) devem monitorar o Quadro de Acompanhamento da Produção com freqüência horária para garantir que os problemas estejam sendo identificados e tratados. O que não foi possível ser resolvido pelo Líder deve ser de responsabilidade deste, e o mesmo deverá utilizar os recursos existentes para eliminar ou reduzir os desperdícios, agindo de maneira planejada e com método (Círculo de Controle da Qualidade, Círculo de Kaizen, Plano de sugestões). Também é o responsável por direcionar as ações do grupo multi-departamental para se resolver os problemas pendentes do quadro e se houver a falha da capacitação da mão-de-obra, deverá elaborar o plano de capacitação das pessoas, definindo a matriz de versatilidade.
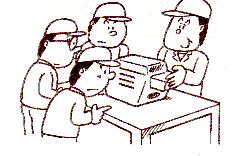
Figura 6: Ensinar, formar os funcionários e fazer kaizens, a função principal do Supervisor
Os Gerentes e Diretores também tem papel importante na resolução dos problemas. Eles devem acompanhar diariamente a produção e o Quadro de Acompanhamento, verificar se as ferramentas e conceitos lean estão funcionando adequadamente (auditorias), e interagir quando problemas não são solucionados.
São também responsáveis por formar as novas lideranças e multiplicadores do conceito, sendo talvez essa a missão mais importante desse nível hierárquico, e devem direcionar e apoiar os Supervisores e seus funcionários, e o grupo multi-departamental na eliminação dos desperdícios e solução dos problemas.
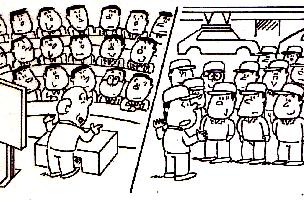
Figura 7: Formar os multiplicadores e garantir a filosofia, a função principal da Direção
O grupo multi-departamental (ver Figura 8), formado pelos responsáveis das áreas de apoio tais como a Qualidade, Engenharia, Planejamento, Logística, Suprimentos, Manutenção, RH e outros, devem fornecer toda a ajuda técnica para se resolver os problemas de forma sistemática e consistente.
O acompanhamento desse apoio deve ser diário, não necessariamente todos ao mesmo tempo, mas rápido, principalmente quando o Andon informa sobre uma parada da área produtiva.
Sob a coordenação do Supervisor ou da Direção, deverão interagir com aqueles problemas apontados no Quadro de Acompanhamento da Produção não solucionados pelo Líder e seus funcionários, pois provavelmente será necessário a utilização de métodos científicos ou detalhados.

Figura 8: Apoio à produção perante as instabilidades, a função principal do grupo
5. O INÍCIO DA CADEIA DE AJUDA E SUAS CONSEQÜÊNCIAS
Todo o processo se inicia quando o Líder realiza a conferência da presença de seus funcionários, cerca de 5 minutos antes de se iniciar a jornada de trabalho. Essa atividade é importante para garantir que a produtividade da empresa seja mantida, pois as perdas com funcionários que chegam atrasado à sua área são consideráveis e acontece na maioria das empresas.
Após a constatação de quem está presente, o Líder através do Quadro Kanri-ban (ver Figura 9) faz a distribuição dos funcionários em função da sua capacitação (matriz de versatilidade) e das necessidades específicas de cada posto de trabalho. Isso é importante, pois o funcionário escolhido de maneira correta possibilita que este tenha condição de iniciar a Cadeia de Ajuda, quando o problema surge. Essa atuação adequada do funcionário normalmente reduz a multiplicação dos problemas, pois é sabido que um problema gerará muitos outros.
O Quadro Kanri-ban contém 2 partes distintas, uma identifica a quantidade de postos de trabalho necessários para cada área produtiva produzir dentro do Takt planejado e os postos específicos que necessitam de pessoas com melhor desempenho. A outra parte mostra quantas pessoas existem naquele setor e sua qualificação mediante a classificação da matriz de versatilidade, e também a identificação de quem esta ausente e a escala dos que estão presentes.
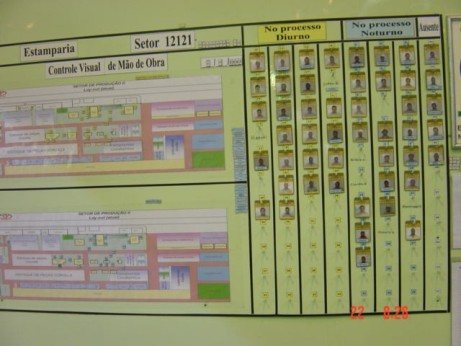
Figura 9: Quadro Kanri-ban
É através do Quadro Kanri-ban que os Líderes também podem promover os treinamentos determinados pela Matriz de Versatilidade, executar os kaizens planejados pelo Supervisor, e até emprestar mão-de-obra para áreas que tenham problemas de absenteísmo, desde que exista mão-de-obra disponível.
A Matriz de Versatilidade (ver Figura 10) é a maneira visual de verificar onde temos o problema de mão-de-obra não qualificada e onde temos processos com deficiência. Também é através dela que temos a condição de formar a multi-funcionalidade, fundamental para se iniciar a Cadeia de Ajuda.
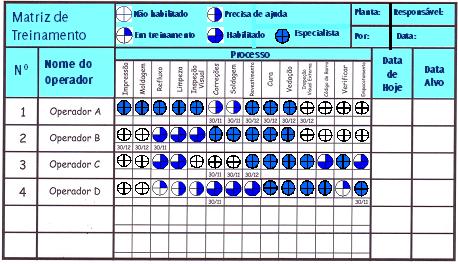
Figura 10: Matriz de Versatilidade
Neste momento da Reunião Diária do Líder, temos o “Primeiro nível da Cadeia de Ajuda”, e quem participa dela normalmente são os funcionários e seu Líder (ver Figura 11), e podendo ter a participação do Supervisor. A escala é feita e também informes e cuidados com assuntos diversos.
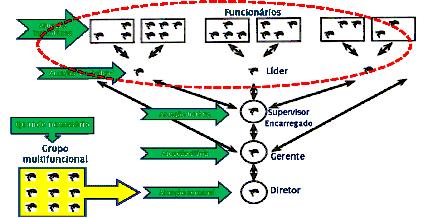
Figura 11: Primeiro nível da Cadeia de Ajuda, a Reunião Diária x Kanri-ban
Após feita a distribuição dos funcionários, o trabalho deve começar rigorosamente dentro do horário, pois numa empresa que implementa o lean e com todas as áreas conectadas, é importante que os processos trabalhem como uma corrente.
Eventualmente problemas vão acontecer durante a produção e precisamos dotar o sistema de uma maneira de avisar onde os desperdícios vão acontecer e quando. Existem duas maneiras de se identificar os desperdícios, ou antes que ele aconteça ou depois.
O conjunto Andon, Jidoka e Pokayoke (ver artigo Jidoka) são importantes ferramentas para se detectar e identificar uma possível anormalidade no processo, e como vimos no artigo sobre “Como operar um Andon” algumas ações devem se iniciar.
Na Figura 12 mostramos que toda vez que o funcionário detectar alguma anormalidade, ele deve acionar o Andon ou outro meio luminoso-sonoro para chamar a liderança, enquanto tenta corrigir o processamento. O Andon acionado (sinal amarelo aceso) informa à diversos setores da fábrica sobre a anormalidade do processo cliente, e tanto o funcionário quanto a liderança (Líder e Supervisor) devem, dentro do Pitch, resolver e impedir a parada da linha.
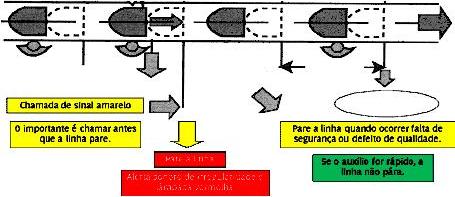
Figura 12: Ações tomadas a partir do Andon
Caso essa ação da Cadeia de Ajuda não resolva ou faça a contenção, um alerta sonoro é acionado pelo Andon e o sinal vermelho ocorrerá, indicando que a produção está parada. Se a capacitação da equipe de funcionários aliado ao conhecimento do Líder e do Supervisor for adequada, a linha não irá parar.
Na Figura 13 vemos o “Segundo nível da Cadeia de Ajuda”, e qual deve ser o envolvimento para esta atividade, da detecção do problema, aviso pelo Andon, e seguido do envolvimento e da ação.
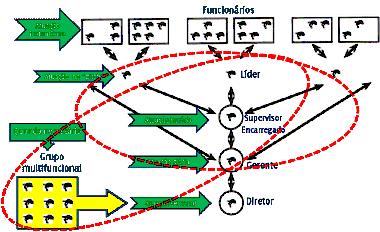
Figura 13: Segundo nível da Cadeia de Ajuda, o Andon x atuação da liderança
O aviso gerado pelo Andon da área onde está acontecendo o problema também gera, em seqüência, avisos para as áreas fornecedoras do componente ou insumos, e até das áreas prestadoras de serviço.
Na Figura 14, mostramos um exemplo de um problema que ocasionou a parada da produção da “Linha de Montagem”, com o seu Andon acionando o sinal vermelho. O Andon da Linha acionará por conseqüência o Andon da área da “Transmissão” (processo fornecedor da Linha de Montagem), que acionará o Andon da área da Usinagem (processo fornecedor da Transmissão), e em certos casos acionará o Andon da Engenharia e da Manutenção, quando esses forem as áreas de apoio para solucionar o problema detectado que originou a parada da Linha de Montagem (processo cliente).
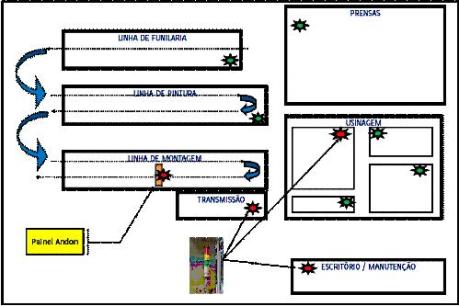
Figura 14: Sistema Andon acionando áreas de apoio
No caso de problemas que paralisam a área produtiva total ou parcialmente durante o dia, as perdas são anotadas no Quadro de Acompanhamento da Produção e os problemas identificados (ver Figura 15).
Temos então nessa fase o “Terceiro nível da Cadeia de Ajuda” (ver Figura 16), onde com freqüência horária o Líder deve analisar e resolver os problemas que se encontram sob a sua responsabilidade, diariamente o Supervisor deve analisar e resolver aquilo que o Líder não conseguiu direcionar, e o Grupo multi-departamental durante o dia intervir e ajudar onde o Supervisor tem necessidades.
A Direção tem a obrigação durante seu Gemba, de conferir se a sistemática da Cadeia de Ajuda está funcionando adequadamente, checando as ações do “Primeiro”, “Segundo” e “Terceiro” nível.
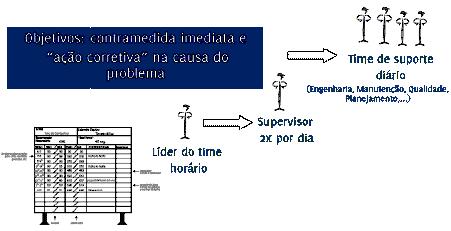
Figura 15: Quadro de Acompanhamento da Produção
Na Figura 16 vemos o “Terceiro nível da Cadeia de Ajuda” e qual deve ser o envolvimento para esta atividade, da detecção do problema pelo Quadro de Acompanhamento, até o envolvimento do grupo multi-departamental.
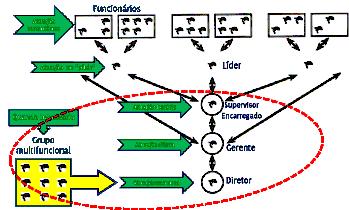
Figura 16: Terceiro nível da Cadeia de Ajuda, o Quadro de acompanhamento x freqüência
6. QUAL O MÉTODO DE RESOLUÇÃO DOS PROBLEMAS
O problema detectado no Quadro de Acompanhamento da Produção deve ter a tratativa mais eficiente e rápida, e por isso devemos determinar qual é o método que será utilizado por cada nível. A sugestão que fica está indicada na Figura 17.
O Líder e sua equipe devem resolver aquilo que está sob sua responsabilidade, e assim atacar os problemas mais fáceis, utilizando métodos como os “5 Por quês”. Para cada problema anotado, preencher um formulário induzindo a se perguntar os por quês até se chegar a causa raiz, tomar a contra-medida e colocar este formulário em um painel ao lado do Quadro.
Os Encarregados e Supervisores devem resolver aquilo que o Líder não resolveu adotando um método mais completo, por exemplo o Gráfico de Ishikawa com os 5 Por quês, ou o PDCA.
Quando houver a necessidade de método mais complexos, o grupo multi-departamental poderá utilizar métodos estatísticos (6 sigma), pois tecnicamente terão mais facilidade e tempo para determinar ações.
A capacitação técnica adequada para cada nível do organograma é importante fator para agilizar a “Cadeia de Ajuda”, além de ser um fator de respeito aos funcionários, pois não podemos exigir sem dar condições de trabalho.
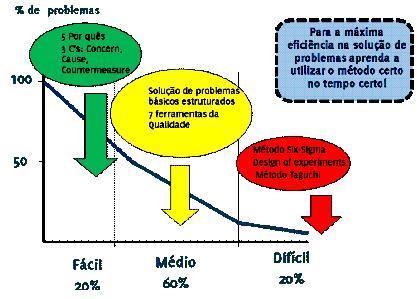
Figura 17: Definição dos métodos de solução de problemas
Uma importante ferramenta para dar assistência à Cadeia de Ajuda é o Quadro Kamishibai, que pode ser utilizado como regularizador das auditorias da Direção, e no auxílio à manutenção autônoma. Neste quadro podemos determinar a priorização de melhorias apontadas pelo Quadro de Acompanhamento da Produção e observações de todos os níveis da Cadeia de Ajuda.
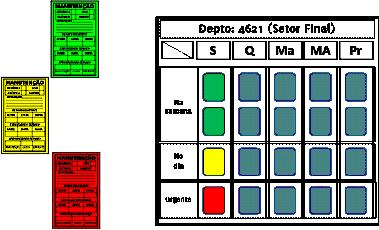
Figura 18: Quadro Kamishibai
Existem outras boas práticas para se auxiliar a Cadeia de Ajuda, tais como a implementação da Cultura do “Plano de Sugestão” (Kaizen Teian) e do CCQ-Círculo de Controle da Qualidade (ver Figura 19).
Alguns dos problemas identificados no Quadro de Acompanhamento da Produção poderão ser direcionados pela liderança, para que os próprios funcionários da área aceitem o desafio de resolverem, com o auxilio da chefia da área. Assim após a implementação o funcionário poderá elaborar a sugestão e enviar para a análise e futura premiação.
A outra maneira de interação dos funcionários para se resolver um dos problemas levantados pelo quadro, é através da atividade do Círculo de Controle da Qualidade. Basicamente essa ação é o resultado da formação de grupos de funcionários da mesma área ou até com a participação de pessoas de outros departamentos, que através da aplicação do método “PDCA” identificam e eliminam as causas raízes.
Tanto o Plano de Sugestão como o CCQ são tipos de sistemática de solução de problemas que auxiliam a Cadeia de Ajuda, e serve também como valorização dos funcionários pela aplicação do conhecimento desses.
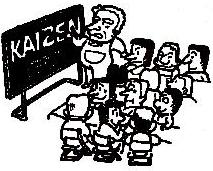
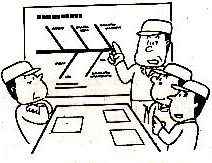
Figura 19: Cultura do Kaizen e o Círculo de controle da qualidade
7. CONCLUSÃO
A estabilidade dos 4M’s são requisitos fundamentais para se iniciar a jornada lean, e a sua manutenção é o que determina a possibilidade de termos os pilares da Casa da Toyota, o “Jidoka” e o “Just in time”.
Essa estabilidade da manufatura somente é alcançada através da identificação e resolução dos problemas, com métodos e responsabilidades definidas, e a “Cadeia de Ajuda” é fundamental como rotina (padrão) de trabalho das pessoas, atuando sempre que surgem anormalidades.
A disciplina é o fator principal para se manter a sistemática da “Cadeia de Ajuda” e assim se tornar um hábito para todos os envolvidos, com a participação da Direção como agentes de auxílio e habilitação dos trabalhos.
Clique aqui para baixar este artigo em PDF versão em Inglês.