A filosofia lean com os seus cinco princípios: valor, fluxo de valor, fluxo contínuo, puxar e perfeição é inspirada no TPS (Toyota Production System).
O TPS constitui um sistema que vai além dos limites das atividades de produção e pode ser aplicado a qualquer atividade onde há um processo definido, isto é, uma seqüência de etapas que têm início, meio e fim. Por exemplo, nas atividades relacionadas a serviços como bancos, seguradoras, atendimentos médico-hospitalar, etc.
Ele teve início na Toyota e seu desenvolvimento foi totalmente ancorado na necessidade. Tem demonstrado ser um sistema que norteia o empreendimento muito eficaz e competente, haja vista o sucesso que a Toyota tem conseguido, como empresa, no cenário mundial dentro de uma das atividades mais competitivas que é o da indústria automotiva.
Para facilitar a compreensão e com finalidade didática estrutura-se o TPS com dois pilares que sustentam o sistema: o JIT (Just in time) e o Jidoka. O Just in time relaciona-se mais ao aspecto quantitativo objetivando manter um fluxo contínuo das atividades em processo, enquanto o Jidoka, o de parar o fluxo quando ocorrer qualquer anomalia. Portanto ele está mais relacionado ao aspecto qualitativo do sistema.
Apesar desta separação, é muito difícil delimitá-los, pois eles inter-relacionam-se e pode-se dizer que o Jidoka complementa o JIT para que o sistema caminhe rumo a perfeição.
1. Jidoka
O Jidoka teve sua origem ligada à automação da máquina de tear
fabricada por Sakichi Toyoda (1867-1930), fundador da Toyoda Automatic Loom Works, considerado um dos dez maiores inventores da história contemporânea do Japão e inventor da máquina de tear automática.
O problema do tear automático era de que;
- A máquina continuava funcionando mesmo diante de um fio rompido e; - O defeito só era detectado quando o processo estivesse concluído, tendo produzido muito tecido defeituoso.
Em tal situação, se um fio rompesse, a máquina produziria tecido com defeito! E para evitar produzir defeito, havia a necessidade de ter um operador tomando conta da máquina como se fosse um vigia e, diante de qualquer anomalia, deveria parar a máquina.
A solução que Sakichi inventou e colocou em prática em 1924 foi uma máquina de tear dotada de dispositivo que parava a máquina quando:
- detectava o rompimento da linha;
- detectava o fim da linha;
- detectava a quantidade programada atingida.
Utilizando-se desses recursos, Sakichi pôde liberar o operador de ficar como vigia tomando conta das máquinas à espera de ocorrência de anomalia.
Eis o que é Jidoka! Dotar a máquina com dispositivos ou recursos que ao detectar qualquer anomalia faz a máquina parar evitando desta maneira produzir a não qualidade como descrito acima.
Mas isto é só uma parte. É o Jidoka que envolve máquina automática. Nem todas as atividades são realizadas pelas máquinas, como por exemplo as atividades de uma linha de montagem, que tem uma intensa participação de atividades manuais. Neste caso como funciona o Jidoka? É o operador quem pára a atividade quando descobre qualquer anormalidade.
Na Toyota operador tem obrigação e o direito de parar a operação quando ele descobrir alguma anomalia e a mesma não for solucionada dentro do tempo takt. Isto faz parte do comprometimento de não passar para operação ou processo seguinte peça ou trabalho com anomalia e isto constitui em uma das regras fundamentais do TPS – a qualidade construída dentro do processo.
A parada é seguida de uma alerta ou sinalização emitida pelo operador através do acionamento de cordões (ou botões) dispostos ao longo da linha de montagem ao alcance dos operadores.
Até aqui foi visto que o Jidoka pode ser tanto aplicado em máquina, como foi a sua origem, assim como para atividades que envolvam somente intervenções humanas.
O objetivo, em ambas situações é detectar qualquer
defeito ou anomalia e fazer parar a operação ou processo para evitar a produção da não qualidade.
Exemplos de Jidoka aplicados a uma linha de montagem:
1. Parafusadeira com “automação inteligente”. Aperto das porcas de fixação da roda no cubo de roda.
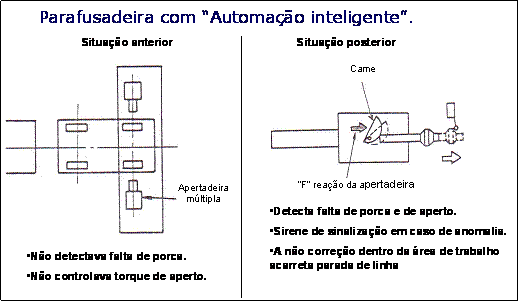
Figura 1a - Exemplo de Jidoka na linha de montagem
2. Torquímetro com micro sensor. Emite sinal sonoro se o equipamento não for utilizado na posição pré-determinada, é uma maneira de assegurar que o torque seja medido garantindo a qualidade dentro do processo.
Figura 1b - Exemplo de Jidoka na linha de montagem
II. Qualidade dentro do Processo
Há alguns anos tem se observado o desenvolvimento e fabricação de máquinas e equipamentos modernos e velozes. Tudo isso é bem vindo, porém vem acompanhado também de problemas.
No caso de ocorrência de pequena anomalia causada, por exemplo, pela entrada de pequeno corpo estranho ou acúmulo de detritos e conseqüente dano à máquina, acaba gerando uma grande quantidade de peças com defeitos. Isto tudo porque a máquina tem grande capacidade de produção, na maioria das vezes automática, que não consegue detectar nem deter peça com defeito e também não é dotada de dispositivo de verificação de anomalia e muito menos com sistema de parar de produzir. Portanto, para garantir a qualidade dentro do processo, a máquina com o conceito de Jidoka deve parar ao detectar qualquer anomalia.
Na Toyota ao adquirir uma máquina ou equipamento muito avançado é de praxe não instalar e utilizar imediatamente. A recomendação é sempre acrescentar algum conceito que incorpore os princípios do TPS e depois utilizá-la. Explicando com mais detalhes, antes de instalar a máquina ou equipamento no “genba”, as equipes de projeto da Engenharia Industrial e Produção executam vários testes, trocam idéias quanto às melhorias e se necessário executam as modificações; só após cumprir esse criterioso preparativo é que a máquina ou equipamento finalmente será colocado em operação.
Mesmo que tenha que parar a linha de produção não se envia peça com defeito para operação ou processo posterior. Ao parar a linha, obviamente ocorrerá perda de produção, mas ao continuar produzindo sem ter encontrado a causa raiz da anomalia, na verdade acabará comprometendo o processo posterior, isto é, acabará afetando diretamente o cliente final com conseqüente perda de credibilidade da empresa.
1. Poka –yoke
Uma das maneiras de se construir a qualidade dentro do processo é através da utilização de dispositivos “à prova de bobeira”, chamados de poka-yoke.
Poka-yoke (à prova de defeitos): dispositivo ou mecanismo simples que instalado na máquina ou no posto de trabalho faz com que se evite a ocorrência de erros, isto é, mesmo que se queira fazer errado o poka-yoke não permite.
Situações em que o poka-yoke tem melhor utilização e contribuição:
Operações manuais que requerem atenção constante do operador;
Onde possa ocorrer o “mau posicionamento”de peça;
Onde for necessário o ajuste;
Onde atributos e não medidas forem importantes;
Onde causas especiais puderem reincidir;
Onde o custo de treinamento e rotatividade for alto;
Em linha onde diversos modelos estiverem em produção;
Onde o custo de falhas externas superar em muito o custo de falhas internas.
Regras para implementação de poka-yoke:
Tomar um processo piloto e fazer uma lista dos problemas mais comuns:
Priorizar os erros por ordem de freqüência;
Priorizar os erros em ordem de importância;
Projetar dispositivos poka-yoke para impedir erros mais importantes das duas listas;
Sempre que economicamente viável, preferir a aplicação dos dispositivos poka-yoke em substituição a outros métodos de inspeção.
Figura 2 - Um exemplo de poka-yoke.
Ao detectar qualquer anomalia o operador deve informar imediatamente ao seu superior. Na Toyota há um ditado: “o trabalho do operador é o de parar a linha”, isto é, eles estão habituados a parar a linha e informar ao superior quando encontram anomalia na produção.
Não obstante não se deve parar a linha imediatamente como a máquina faz, deve-se primeiro alertar que vai parar e só depois de um tempo determinado (tempo takt) é que deve parar, isto ajuda a não deixar a operação pela metade. Para executar essa sistemática foi idealizado o “sistema de parada em posição determinada”. A ferramenta mais comumente usada para sinalizar a parada em posição determinada é o “andon”.
2. Andon
Trata-se de um painel indicador de parada de linha que fica instalado na parte superior, próximo ao teto do “genba” para que seja visível por todos.
Os indicadores do painel são acionados quando cordões são puxados ou botões são acionados. Então, acende-se a luz amarela que é um aviso de que a linha vai parar caso não se resolva o problema ou anomalia. E em não sendo solucionado, a linha pára em uma posição determinada e quando isso acontece acende-se uma luz vermelha no “andon”. Portanto, “andon” é uma ferramenta que permite ao operador parar a linha ao encontrar uma anomalia e permite buscar ajuda para solucioná-la.
Na Toyota o operador tem autonomia para parar a linha e ele é responsável em manter a qualidade dentro do raio de sua operação e jamais enviar peça com defeito ao processo posterior. Essa atitude e comprometimento são o que sustentam da alta qualidade dos produtos Toyota.
A ferramenta que informa anomalia na linha de produção não precisa ser necessariamente o “andon”. Em fábricas de pequeno porte não é preciso ter necessariamente o “andon”, pois normalmente como há poucos processos e máquinas, o próprio operador pode detectar facilmente a anomalia. Como “andon” é uma ferramenta de anunciar uma anomalia, se houver qualquer dispositivo que possa executar essa função não há problema algum; pode ser um alarme sonoro ou mesmo sinaleiro de luzes intermitentes.

Figura 3 – Exemplos de “andon”.
A idéia básica é de que seja qual for a anomalia: atraso na operação, problema no equipamento, problema de qualidade, etc, o operador não deve ficar com dúvida e deve parar imediatamente a fim de não produzir a não qualidade e partir para análise da causa raiz do problema.
Comumente o que mais tenho observado nas empresas, é que mesmo que se detecte anomalias na qualidade durante a operação, por temer a queda na produtividade com parada de produção, faz-se vistas grossas, segregando a peça com defeito e ou inspecionando no final e executando reparos. A qualidade tem que ser construída e garantida dentro do próprio processo. Portanto, pare ao encontrar anomalia, seja qual for a operação manual ou a máquina. É muito importante preservar este conceito fundamental no TPS.
3. Trabalho Padronizado
Interpretar como anomalia tudo que não estiver de acordo com o Trabalho Padronizado. Para entender o que é anomalia, há a necessidade de definir o parâmetro de o que é anormal e esse é o papel do Trabalho Padronizado. No caso de máquina, instala-se um dispositivo que a máquina pára ao detectar qualquer anomalia, mas no caso de operação manual define-se o Trabalho Padronizado, e caso ele não seja seguido na íntegra, pára-se a linha.
O Trabalho Padronizado é composto por três elementos: tempo takt, seqüência de atividades do operador e estoque padrão de processo. Ele está baseado na melhor utilização da disponibilidade do operador e o que dá a sustentação do TPS quanto à produtividade, qualidade e segurança no trabalho, inclusive. Constitui-se numa ferramenta essencial para manter a produção estável.
III. Produtividade
No início da década de 1950, Sr. Taiichi Ohno (1912-1990), o pai do TPS, entra em ação. Foi ele que, naquela época, quando a Toyota enfrentava grandes dificuldades deparou-se com o problema da necessidade de aumentar a produtividade na área de usinagem, da qual era o gerente.
O Sr. Ohno observou que era improdutivo a presença de um operador fixo por máquina. A solução foi de fazer mudança no layout para o sistema em que um operador pudesse operar mais de uma máquina. Obviamente, para realizar isto as máquinas deveriam estar dotadas com os conceitos de Jidoka.
Carregar a máquina com mínimo de trabalho possível, reduzindo a carga de trabalho do homem e empregando-o em outras atividades que só pudessem ser executadas por ele. Ao atribuir à máquina automática a característica do Jidoka, muda-se radicalmente o método de controle das máquinas e equipamentos. Não há necessidade do operador ficar vigiando a máquina enquanto esta estiver trabalhando; só será necessário o operador dirigir-se à máquina quando esta parar devido a alguma anomalia.
Nos dias de hoje, existem máquinas automáticas com dispositivos que ejetam peças com defeito. No passado, era normal uma máquina ser monitorada por um operador que retirava as peças com defeito. A introdução desse dispositivo, dotado com capacidade de julgar o defeito e ejetar as peças, evitou a necessidade desse operador ficar como vigia, mas não eliminou a produção da não qualidade. Portanto, é importante entender essa diferença do Jidoka.
No Jidoka a máquina pára ao detectar alguma anomalia e sinaliza que está com problema. Isso evita produzir a não qualidade ao mesmo tempo em que um operador é capacitado de monitorar várias máquinas. Em outras palavras, com o avanço do Jidoka não haverá mais necessidade de “vigilantes” ao lado das máquinas. Ao eliminar a tarefa de vigilante de máquina, há uma grande oportunidade para treinar os operadores para serem multifuncionais capacitados a trabalhar com várias máquinas de diferentes processos.
Simultaneamente a racionalização da mão-de-obra na Toyota, aos mais veteranos é atribuída a missão de serem especialistas em execução de kaizens que garantam qualidade dentro do processo.
Na execução de kaizen de qualidade normalmente, demanda-se tempo e existem casos que vão se arrastando sem conseguir resultados. Esses kaizens são executados pelos próprios operadores e há casos em que eles por si não conseguem resolver, e que só é possível de ser resolvido no nível gerencial.
Em todas as plantas existem problemas dessa natureza, e aos veteranos que ficam alocados como especialistas assessores do gerente é designada a missão de resolver esses problemas.
A produtividade pode ser aumentada através de medidas que evitem a recorrência de situações anômalas. Uma vez detectada alguma anomalia, ir fundo na causa-raiz para resolver de vez e evitar a recorrência.
Com Jidoka, a máquina pára ao detectar uma anomalia. Nessas ocasiões, deve-se analisar com muito cuidado o motivo da parada, trabalhar imediatamente na elucidação da anomalia e dedicar-se às ações para evitar a recorrência.
Abaixo um exemplo do uso do método PDCA que com a sistemática de cinco porquês busca a causa-raiz:
Supondo-se que: “O interruptor se soltou”.
Questione: “Porque o interruptor se soltou?”.
Ao verificar a causa: “É porque não houve aplicação correta do lubrificante”.
Aprofundando no questionamento:
“Porque não houve aplicação correta?”.
“É porque não há procedimentos”.
“E porque não há procedimentos?”.
E assim, questionando as respostas obtidas com sucessivos porquês, busca-se a causa-raiz do problema, executam-se os kaizens e padronizam-se os procedimentos. Basicamente o que se faz é a repetição contínua desse procedimento. Os operadores devem ser condicionados a questionar toda e qualquer situação. Não só as ocorrências de anomalias, mas também as situações em que se obtém sucessos, questionando “porque deu certo?”.
Para finalizar, o importante é fazer a prática do uso desses conceitos sempre no “genba”, onde as coisas estão acontecendo e não ficar divagando na mesa do escritório. Isto é, fazer o genchi-genbutsu.
Referências Bibliográficas:
Apresentação do Jidoka no Lean Summit 2006 por G.I.Kosaka
Toyota Production System: An Introduction. Masamitsu Ishii, 2005
Toyota Production System. Toyota Motor Corporation, 1977