O prazo ou “lead time” desde a concepção do produto até o lançamento no mercado é um dos fatores mais importantes para garantir a capacidade competitiva de uma empresa e ampliar suas possibilidades de expansão de mercado. Pode definir se a empresa vai ser a pioneira ou uma seguidora rápida em determinados segmentos ou nichos de mercado.
O conceito de padronização é utilizado na manufatura para manter a estabilidade nos processos, garantindo que as atividades sejam realizadas sempre numa determinada seqüência e da mesma forma, num determinado intervalo de tempo e com o menor nível de desperdícios, conseguindo elevada qualidade e alta produtividade. É a base para realizar as futuras melhorias, eliminando mais desperdícios e encurtando ainda mais o lead time.
A aplicação da padronização no desenvolvimento de produtos também proporciona uma redução significativa no “lead time”, pois evita a ocorrência de desperdícios como esperas, buscas e correções de informações que provocam retrabalhos, tanto na área de projeto como posteriormente, na manufatura.
Neste artigo é apresentado um método para realizar o “kaizen” no desenvolvimento do produto, em particular, para a redução do “lead time” através da utilização do conceito de padronização.
1. Identificando os produtos com os maiores “lead times”
Em primeiro lugar, devemos identificar qual produto possui o maior “lead time” de desenvolvimento para posteriormente analisar como reduzi-lo. Consideraremos “lead times” para a mesma categoria ou natureza de desenvolvimento, por exemplo, pequena, média ou total alteração no produto.
Podemos identificar os tipos de produtos e seus respectivos “lead times” de desenvolvimento quando possivelmente poderemos ter um gráfico semelhante ao abaixo:
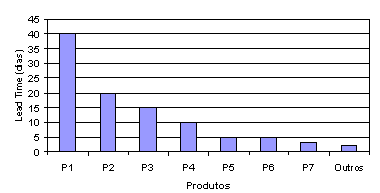
Gráfico 1 – “Lead Time” por produto
Notamos que o produto P1 possui o maior lead time de projeto. Geralmente são aqueles produtos mais complexos, possuindo diversos sub-componentes.
A definição do produto com o maior lead time pode ajudar a priorizar os esforços de melhoria. Outros fatores econômico-financeiros e estratégicos podem ser igualmente importantes na definição do produto a ser enfocado, mas a existência de elevado lead time tende a significar relevância e alto custo.
2.
Identificando as atividades envolvidas
Identificado o produto (ou família de produtos), deveremos então identificar* as etapas ou processos pelo qual este produto passa. De uma forma macro, podemos citar como exemplo o caso abaixo, apenas listando as atividades e seus “lead times” respectivos, conforme mostra a tabela 1.
|
Atividades |
LT (dias) |
1 |
Reunir com cliente |
1 |
2 |
Aprovar especificações |
2 |
3 |
Realizar projeto básico |
5 |
4 |
Gerar desenhos para aprovação |
8 |
5 |
Inspecionar desenhos |
1 |
6 |
Corrigir desenhos |
5 |
7 |
Aprovar desenhos do projeto básico |
1 |
8 |
Gerar desenhos detalhados |
15 |
9 |
Inspecionar desenhos |
1 |
10 |
Aprovação dos desenhos finais |
1 |
|
TOTAL: |
40 |
Tabela 1 – Atividades para o produto 1
3. Analisando as atividades de maior “lead time”
Representando os processos macros e seus “lead times” em ordem decrescente, observamos que a etapa 8 (Gerar desenhos detalhados) e 4 (Gerar desenhos para aprovação) representam quase 60% do “lead time” total.
Se analisarmos com mais detalhe as atividades de geração de desenhos, notamos que a proporção da quantidade de desenhos reutilizados, ou seja, aproveitando-se arquivos de projetos anteriores e aqueles feitos completamente do zero, podemos observar o seguinte resultado abaixo:
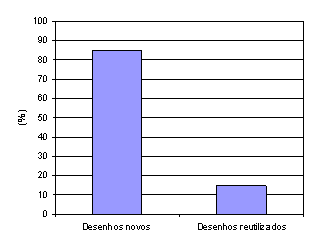
Gráfico 2 – Desenhos novos x reutilizados
Perguntamos então por que há necessidade de geração de tantos desenhos novos, por que a taxa de reutilização de desenhos é baixa e se não seria possível reduzir este esforço que consome tanto tempo e recursos sem prejudicar a qualidade do desenvolvimento. Quase sempre se chega à conclusão de que a falta de padronização em certas especificações técnicas leva os projetistas a realizarem um novo desenho a cada novo produto desenhado.
4. Plano para padronização
Deste modo, julgamos necessário um esforço para aumentar a padronização para aumentar a taxa de reutilização de desenhos e com isso reduzir o “lead time” total.
Para isto, é importante obter o apoio dos projetistas mais experientes para realizar um plano para a padronização das especificações técnicas como, por exemplo, dimensões de cotas, tolerâncias e definir quais itens serão padronizados. A figura 1 representa uma peça modelo com suas cotas A, B, C, D, E, F e G.
Em seguida, procuramos criar tabelas de cotas com dimensões padrões (tabela 2) para os diversos componentes possíveis, baseados em estudos utilizando ferramentas como diagramas de relações entre estas cotas (gráfico 3).
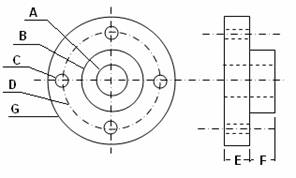
Figura 1 – Peça modelo
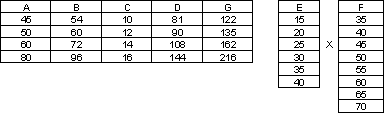
Tabela 2 – Tabela de dimensões padrões
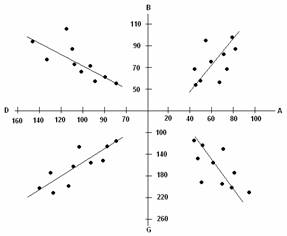
Gráfico 3 – Diagrama de relações entre cotas
Com isto, pode-se gerar um banco de dados dos modelos em CAD com dimensões padrões. A figura 2 representa os desenhos padrões em CAD à disposição, sem precisar redesenhá-los. O objetivo é não desenhar o componente a cada novo produto, mas sim, copiar e colar aproveitando estes modelos padrões, reduzindo-se assim, o lead time na execução dos novos desenhos. Quanto mais padrões possuir, menos tempo será a etapa de gerar desenhos para a aprovação ou a execução de desenhos detalhados. Auxiliará também na fase da manufatura inclusive em termos de setup de máquinas, pois diminuem os tempos para ajustes desnecessários a cada novo produto.
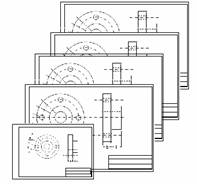
Figura 2 – Modelos padrões em CAD
No caso de indústrias químicas, alimentícias e as demais que não utilizam desenhos detalhados para a fabricação dos produtos, pode não caber a padronização de medidas, mas sim padronizar especificações e informações técnicas sobre formulações, embalagens entre outras.
5. Outros tipos de padronizações
O motivo da ocorrência de longos “lead times” é a existência de desperdícios nas atividades do processo de desenvolvimento. Um dos desperdícios mais comuns é o tempo gasto para buscar informações, principalmente especificações técnicas em falta, enviados pelo departamento de Vendas após a negociação com o cliente. Muitos retrabalhos acontecem quando os projetistas seguem o projeto com especificações pressupostas devido à falta delas.
Outro desperdício freqüente é o retrabalho gerado quando os desenhos chegam à Produção com especificações que não são compatíveis para a manufatura. Isto acontece devido à aceitação por parte de Vendas de pedidos com especificações personalizadas dos clientes, sem consultar o departamento de Desenvolvimento e Manufatura sobre suas implicações no desenvolvimento do produto.
Para eliminar estes retrabalhos e perdas de tempos, deve-se melhorar ou criar formulários para requisição de pedidos, padronizando certos campos. Prepare um manual para o pessoal de vendas com as especificações pré-estabelecidas dos produtos com padronizações já incorporadas. Realize treinamentos e reuniões entre o pessoal de Desenvolvimento e Vendas para explicação destas padronizações.
Muitos podem argumentar que os retrabalhos, ou as mudanças de especificações durante o projeto são atividades que agregam valor, pois o esforço é feito, em muitos casos, para melhorar o desempenho do produto final. Entretanto, estas ações causam diversos tipos de desperdícios tanto para a empresa como para seus fornecedores. Por exemplo, geram:
1. Materiais que não são mais utilizados;
2. Componentes que se tornam obsoletos;
3. Substituição dos ferramentais para atender as novas especificações do produto;
4. Esperas pelas emissões de novos pedidos de itens;
5. Esperas pelas novas entregas;
6. Remontagens do novo componente ou produto;
7. Reinspeções;
6. Mensurando e acompanhando o “lead time”
Só conseguimos melhorar algo quando podemos mensurá-lo. Um dos indicadores importantes a ser mensurado é o Acompanhamento dos Prazos, dado pela relação:
Lead time alvo de projeto
Lead time atual de projeto
Isto porque na fábrica, uma linha de produção inteira pode parar por necessidade de um único desenho faltando. Se este valor for igual a “1”, o andamento do projeto está em dia. Para valor menor que “1”, significa que o projeto está atrasado e valor maior que “1”, adiantado.
7. Conclusão
A padronização das especificações de componentes no processo de desenvolvimento é um dos elementos mais importantes para a redução do “lead time”. Serve para eliminar os ruídos e desperdícios gerados durante o desenvolvimento de produtos.
Os passos apresentados neste artigo podem ser úteis para enxergar e expor os desperdícios, atacar a causa raiz podendo beneficiar tanto o processo de desenvolvimento do produto reduzindo o lead time do desenvolvimento e como conseqüência os custos totais. Estas práticas podem ser consideradas como um passo básico para muitas empresas, semelhante à estabilidade básica (5S, melhoria da disponibilidade de máquinas etc) que são necessárias no início de uma transformação lean na manufatura.
Uma abordagem mais ampla, dando continuidade a este esforço, incluiria a utilização do mapeamento de fluxo de valor nos processos de desenvolvimento do produto e inclusão, no estado futuro, de elementos do sistema lean de desenvolvimento, como por exemplo, a engenharia simultânea com múltiplas alternativas (set-based concurrent engineering), liderança de projetistas de sistemas com espírito empreendedor, planejamento descentralizado com cadência e fluxo puxado, interações freqüentes entre as equipes de especialistas responsáveis em que o foco é na criação de um fluxo de valor lucrativo e conhecimento reutilizável que atenda às necessidades dos clientes.
Bibliografia
*Para maior aprofundamento em como desenhar o mapa do fluxo de valor para desenvolvimento de produtos, vide Liker, J. K. e Morgan, J. M. The Toyota Product Development System: Integrating People, Process And Technology, Productivity Press, 2006.
Kennedy, M. N. Product Development for the Lean Enterprise, Oaklea Press, 2003.
Marchwinksy, C e Shook, J (cords). Léxico Lean. Lean Institute Brasil, 2003.
Sekine, K., Arai, K. Design Team Revolution, Productivity Press, 1994.
Ward, A. C. The Lean Development Skill Book. Ward Syntesis, 2002.