Uma das maiores barreiras para a solução de problemas A3 em muitas empresas norte-americanas é que, normalmente, existem poucas ou nenhumas medidas e padrões de desempenho no nível do processo. A maioria das empresas tem KPIs (indicadores-chave de desempenho), mas geralmente são resultados operacionais ou medidas no final de processo. Eles também são “indicadores de atraso”, porque mostram o resultado do trabalho executado, mas não o quão suave e eficientemente o trabalho está fluindo no processo – a menos que eles falhem em atingir os KPIs de saída. Sem processos ou padrões de trabalho, aqueles que concluem o processo não têm como avaliar o seu desempenho ou onde focar na solução de problemas quando há problemas nos resultados de produção.
A situação na Toyota, onde o processo A3 se originou, é bem diferente. Eles têm um ditado: “Sem padrão; sem problemas”, o que para eles é verdade. Se há um ponto em que a empresa precisa medir o desempenho para gerenciá-lo ou melhorá-lo, eles têm padrões para o que deve estar acontecendo. Eles têm medidas de desempenho que começam no nível de operação individual, incluindo processos e procedimentos definidos. E há um rastreamento com base nesses padrões que vai desde a equipe até os níveis de grupo, área, departamento, operação e empresa. Na área de operações de manufatura, por exemplo, os sinais digitais exibem o número de veículos produzidos em comparação ao planejado em qualquer ponto durante um turno.
Não ter padrão pode não ser um problema para a Toyota, porque eles criaram ou irão criar padrões de desempenho e padrões de trabalho onde precisarem deles. Mas, para muitas empresas com as quais trabalhei, esse não é o caso – é um problema, um grande problema. Sem padrão, não há como ver quais melhorias precisam ser feitas para melhorar o desempenho ou ver o impacto das mudanças que foram feitas. É difícil melhorar em uma base de caos. Você pode fazer mudanças, mas com a confusão, a desordem e a instabilidade, como você pode saber se está indo na direção certa? Como você pode saber se está fazendo a diferença em uma situação caótica e instável?
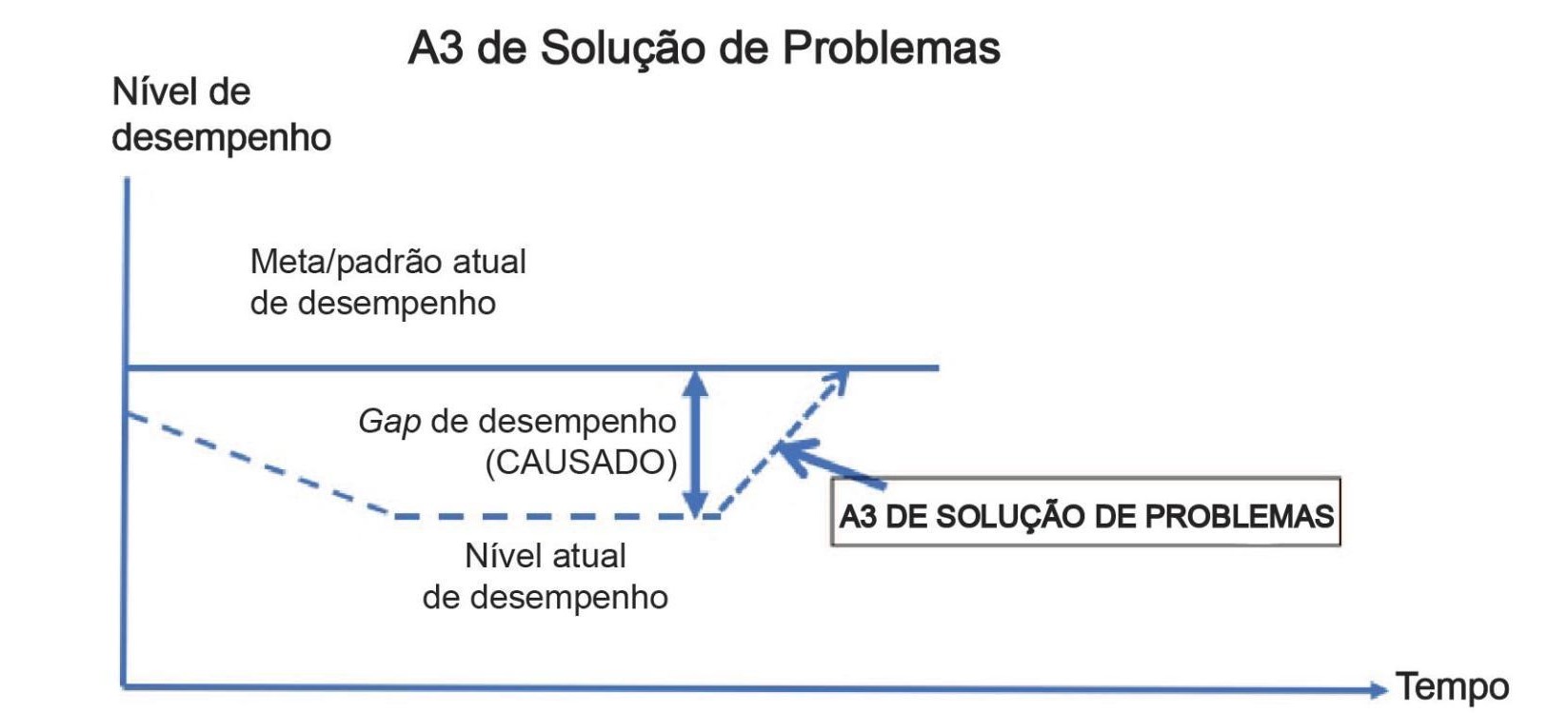
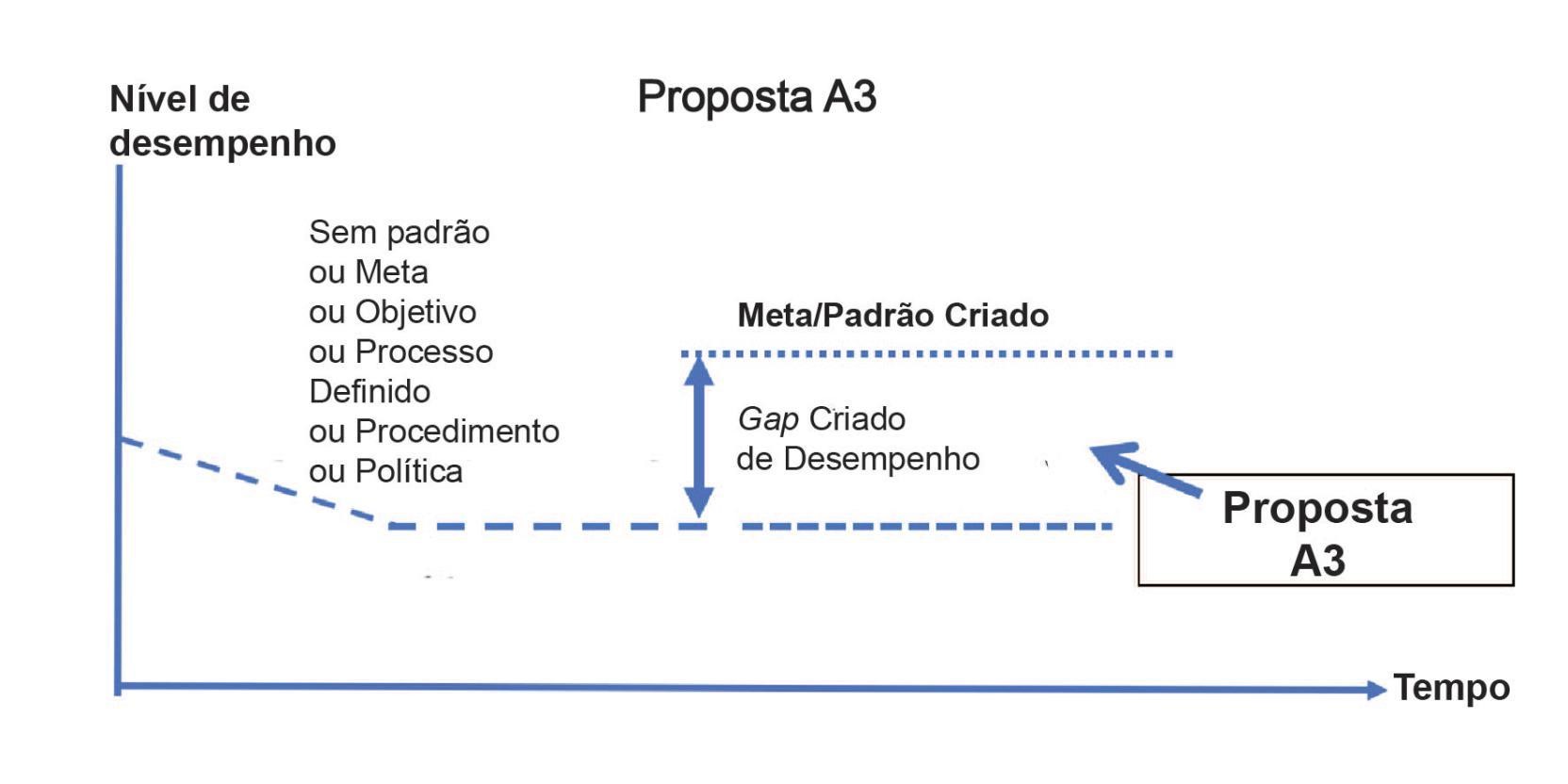
Em situações em que há meta ou padrão de desempenho que não está sendo alcançado, um A3 de solução de problemas é usado para fechar a lacuna. Em situações em que um problema ou necessidade é reconhecida, mas não há uma meta ou padrão de desempenho, uma proposta A3 é usada para definir um.
Uma melhoria em uma situação instável é como uma gota no oceano. Faz respingos, mas desaparece muito rapidamente. O princípio fundamental do pensamento lean, da melhoria contínua e da melhoria de desempenho, que aprendi ao longo dos anos, é primeiro estabilizar da melhor maneira possível, padronizar o máximo possível e depois trabalhar para melhorar.
Recentemente, vi um exemplo da confusão causada por padrões pouco claros quando estava treinando um gerente de engenharia. Ele era o líder de um grande projeto de desenvolvimento de um novo produto para um cliente. Ele estava frustrado com seus engenheiros por causa do tratamento das mudanças de engenharia. Depois que o design do produto foi definido no plano original, os engenheiros aprenderam algumas coisas ao desenvolvê-lo que tornaram as mudanças necessárias. O problema, para o gerente, era que os engenheiros de projeto frequentemente se atrasavam para enviar essas alterações ao cliente. E as mudanças tardias significavam penalidades para sua empresa.
O contrato especificava o tempo no cronograma pelo qual as alterações de engenharia deveriam ser enviadas ao cliente. Quando as alterações não eram aprovadas a tempo, o custo original era aplicado, e a produtora tinha que absorver a diferença, que geralmente era maior. O gerente de engenharia lembrava seus engenheiros sobre isso com frequência e não conseguia entender por que as mudanças costumavam atrasar. Sugeri que acompanhássemos o processo e falássemos com os engenheiros para descobrir o que estava acontecendo.
Iniciamos pelo final do processo, quando os engenheiros submetiam as alterações a uma equipe que coordenava o cronograma mestre e as enviava para a empresa cliente. Aprendemos com a responsável pelo encaminhamento das mudanças que mais de 50% estavam atrasados, o que gerava trabalho extra para ela. Perguntei sobre o processo de trabalho, e ela disse que os engenheiros têm muitas responsabilidades diferentes no projeto, e todos eles sabem que essa é uma das coisas que deveriam fazer.
Sugeri que conversássemos com os engenheiros. Descobrimos que a maioria dos engenheiros encarregados de fazer mudanças na engenharia eram jovens, relativamente inexperientes e novos na empresa. Eles não foram treinados ou não receberam orientações sobre como fazer as mudanças de engenharia. Mais importante, eles precisavam de informações sobre os custos das mudanças, mas não tinham experiência para calcular. E eles não foram informados sobre onde poderiam obter essas informações com o departamento de estimativas. Muitos deles disseram que ficavam com medo de errar nas estimativas. É por isso que geralmente demoravam a enviar as solicitações de mudança.
No lean, falamos sobre a importância dos padrões e como eles são necessários para esclarecer problemas e gerenciar o desempenho. E geralmente pensamos nos padrões como metas, objetivos e KPIs. Mas processos, procedimentos e um fluxo de trabalho definido também são padrões; eles são padrões de trabalho. O trabalho padronizado da Toyota é um exemplo bem definido. Se você estabelece metas e não dá às pessoas um caminho bem definido que elas podem seguir para alcançar esses resultados, você não as está tornando capazes de ter o desempenho que deseja. Você não tem uma meta ou um padrão. Você está apenas esperando que elas obtenham os resultados com seu esforço.
O gerente de engenharia percebeu que era responsável por desenvolver os processos que queria que seu pessoal seguisse e treiná-los para ter certeza de que sabiam como usá-los.
Atingindo um acordo sobre um padrão
Fundamentalmente, um padrão é uma declaração que diz que concordamos sobre como as coisas deveriam ser (ou como precisamos que elas sejam) em uma situação de desempenho. Ele especifica o que é esperado em determinada situação de trabalho. Mas um padrão não é eficaz como uma expectativa que guiará o comportamento a menos que seja acordado, documentado e comunicado. Sempre que possível, um acordo sobre um padrão ou meta deve ser alcançado com aqueles que devem cumpri-lo.
Vi um exemplo disso em um departamento de Recursos Humanos onde eu era consultor. Fui convidado para treinar um especialista de RH recém-contratado que estava tendo dificuldades em seu primeiro grande projeto. Ele deveria ministrar treinamento para supervisores sobre uma política revisada que eles deveriam implementar, e a participação estava muito baixa.
Embora relativamente novo na empresa, ele era responsável por atualizar uma importante política de benefícios aos colaboradores e ensinar gerentes e supervisores sobre como desempenhar seu papel na execução da política. Esse jovem especialista era brilhante e havia feito pesquisas sólidas sobre as mudanças políticas exigidas pela legislação recente. Ele também criou um programa eficaz para informar os líderes sobre as mudanças e mostrar-lhes como ajudar os colaboradores que se qualificam para os benefícios. Ele até fez seu primeiro A3 e traçou um plano para implementar o treinamento. Ele me conduziu pelo lado esquerdo do A3, e entendi o que ele estava tentando realizar.
Quando ele descreveu o lado direito de seu plano, perguntei se todos concordavam com o cronograma que havia sido estabelecido ali. Sua resposta foi que sim, que o gerente e o vice-presidente aprovaram. Perguntei se a gestão dos supervisores que precisavam participar do treinamento (principalmente os gerentes de produção) também havia concordado com o plano. Ele disse que sim, que tinha certeza que sim. Isso me levantou certa desconfiança. Olhei para o cronograma de treinamento e analisei-o com ele. Observei que ele tinha sessões suficientes para cobrir por todos os supervisores. E na coluna “Responsável”, ele listou os gerentes do outro departamento como responsáveis junto com ele.
Perguntei como ele conseguiu seu apoio com a preparação para o lançamento do novo modelo que estava acontecendo ao mesmo tempo. Ele respondeu que tinha certeza de que fariam a parte deles e apoiariam o treinamento. É responsabilidade deles, disse ele. Minha dúvida era se ele havia concordado com o cronograma de treinamento. Bem, não diretamente, disse ele. O comitê executivo aprovou o treinamento.
Perguntei se eles tinham visto a programação, e ele disse que não; ela não estava pronta quando eles revisaram a política. Então, perguntei como ele planejava obter o apoio dos gerentes para melhorar a participação, agora que está fazendo o treinamento e recebendo poucos participantes.
A resposta foi um silêncio de dois ou três minutos. Então, ele me disse que havia enviado um e-mail um mês antes do início das sessões dizendo que o treinamento era obrigatório e que era responsabilidade deles garantir que seu pessoal comparecesse. Ele acrescentou que vai lembrá-los de que a lei exige que eles completem o treinamento e que os executivos o aprovem.
Sugeri que ele precisava testar a ideia de que eles realmente concordaram com o cronograma. Pedi que ele fosse a cada chefe de departamento ou gerente que ele listou como responsável, que lideravam pessoas que precisavam comparecer, com um plano atualizado com seções adicionais. Pedi a ele que assinasse a coluna de responsabilidade para indicar que os líderes apoiariam agendando a presença de seu pessoal.
Não tive mais notícias dele por cerca de três semanas. Eu esperava que ele estivesse na fábrica conversando com as pessoas e aprendendo duas coisas: primeiro, você não pode simplesmente deixar a responsabilidade para outras pessoas. Você deve certificar-se de que isso funciona para a situação e as prioridades deles para que eles possam aderir. E, em segundo lugar, você tem que entender o contexto mais amplo do que mais está acontecendo na empresa quando você pede um acordo sobre um plano.
Existe um termo em japonês, nemawashi, que se traduz como “preparar o terreno para o plantio”. Nemawashi é uma prática padrão na Toyota para construir uma base de acordo com o propósito, o processo, o plano e a responsabilidade para obter suporte para uma iniciativa de melhoria, projeto ou solução de problemas A3. Na semana seguinte, o especialista de RH me disse que havia chegado a um acordo com os gerentes sobre uma programação revisada que começaria após a mudança do modelo.
O A3 não é apenas uma ferramenta para relatar atividades de solução de problemas, buscar a aprovação de contramedidas e executar um plano. Na Toyota, é parte do processo para liderar a mudança e atender às necessidades da operação e do negócio. É uma ferramenta para documentar o que é aprendido sobre como melhorar o desempenho e obter acordo e suporte para as mudanças necessárias.
O processo A3 é um processo técnico de solução de problemas com base no ciclo Planejar-Executar-Verificar-Ajustar. É também um processo social de envolvimento e escuta e de incorporação de seu conhecimento e pensamento no desenvolvimento de um plano de mudança. A chave para todo o processo é que, por meio dele, o líder da mudança obtém acordo e suporte, porque reflete as melhores opções, métodos e tempos disponíveis para a situação de todos.
O processo A3 funciona porque a Toyota treina seus líderes para usá-lo, e todos sabem que é assim que se lida com problemas e se faz melhorias para o bem dos negócios. Em outras palavras, é o trabalho padrão da Toyota para resolver problemas, iniciar melhorias e liderar mudanças.