Muito se fala sobre a otimização dos sistemas de desenvolvimento de produtos existentes e apesar de se tentar interpretar e aplicar as técnicas de desenvolvimento lean, empresas e corporações ainda se vêem com os tradicionais problemas de qualidade nos desenhos, longo ciclo de desenvolvimento de produtos, cronogramas de lançamento pouco confiáveis e conseqüentes altos custos de desenvolvimento final.
Para obter sucesso neste processo, o desenvolvimento “enxuto” deve ir além das técnicas convencionais da conhecida engenharia simultânea, trabalhos de engenharia padronizados ou mesmo estruturas organizacionais que designam fortes gerentes executivos de projeto para a função.
O processo de desenvolvimento para se tornar realmente “lean” deve focar na efetiva criação de “fluxos de valor operacional” ao longo do ciclo de desenvolvimento, os quais se mostrem realmente lucrativos e, além disto, entender que a criação do conhecimento reutilizável será chave para atingir isto de forma mais eficiente, previsível e eficaz.
FLUXO DE VALOR ENXUTO
Mas afinal, o que vem a ser um bom sistema de desenvolvimento de produtos e como definir os fluxos de valor ao longo do desenvolvimento? Certamente esta é uma questão bastante complexa, cuja resposta podemos explorar olhando mais a fundo para o modelo desenvolvido pela Toyota, que como se sabe tornou-se benchmark no que se refere à velocidade nos lançamentos, qualidade nos desenhos (voltados para a manufatura e montagem), custos competitivos, além de possuir inquestionável produtividade na integração dos projetos.
O fator chave para que isto ocorresse foi que a Toyota conseguiu enxergar o desenvolvimento de produtos como um processo repetitivo e que pode ser continuamente aperfeiçoado. E ela vem fazendo isto de forma sistemática ao longo dos anos, projeto a projeto, desde que assimilou os conhecimentos de W.E. Deming a partir da década de 50.
O Ciclo Deming ( ou PDCA ) associado ao ciclo do aprendizado
Análise dos termos associados à Manufatura Lean quando comparados ao Desenvolvimento
Manufatura Desenvolvimento do Produto
Matéria-prima - Conhecimento.
Fluxo - Cadencia de informações ao longo do ciclo de desenvolvimento.
Sistema puxado - Metodologia eficiente, conectada (bom sistema de Gestão de Projetos).
Valor - Somatória positiva de todos os fatores aqui descritos.
Perfeição - Reutilização continua do conhecimento retido.
Gemba - Obeya (ocasião e local onde se reúnem simultaneamente todos os envolvidos no projeto).
Andon - Relatório A3.
Reduzindo desperdícios no desenvolvimento
A base que sustenta o princípio lean é o da redução dos desperdícios ao longo de um processo, tornando-o um fluxo operacional de valor. Se fizermos uma analogia dos fluxos na manufatura e compará-los ao ciclo de desenvolvimento de produtos, podemos associar diversas formas de desperdício:
Retrabalhos: testes que atrasam em relação ao cronograma, existência da necessidade de revisão em reuniões exaustivas com os executivos para se avançar com o projeto, interrupções outras diversas, falta de qualidade na fonte da informação.
Espera: requerimentos faltantes nos desenhos, falta de aprovação no tempo certo, desalinhamento funcional da organização, entre outros.
Super-processamento: de informações e relatórios diversos e às vezes ferramentas que se sobrepõem, sistemas informatizados, requisições múltiplas de aprovação, procedimentos redundantes, sistemas complexos de TI, entre outros.
Inventário de conhecimento e informações: lotes de desenho aguardando liberação em alguma etapa do processo, falta de ciclos curtos de aprendizado e repasse do conhecimento adquirido.
Produção em excesso: informações e relatórios excessivos e redundantes, planejamento mal executado, entre outros.
Movimentação física: busca de informações , reuniões inúteis, etc.
Movimentação de informações: informações a serem re-digitadas, múltiplas base de dados, grandes arquivos e relatórios em Excel difíceis de se manipular, apresentações complexas que devem ser refeitas, etc.
Notaram alguma relação com a famosa “Ponta do Iceberg” ?
Desenvolvimento LEAN de Produtos: Uma Visão Sistêmica
Fonte : J. Luckman Consulting
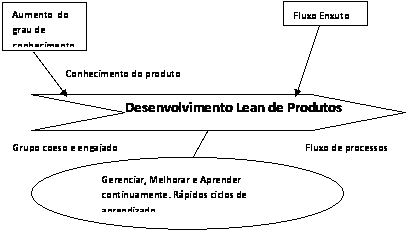
Diversos acadêmicos da “escola lean” nos Estados Unidos concluíram em seus estudos que um dos fatores chave para o sucesso japonês deriva do eficiente processo de integração entre o desenho do produto e do processo, incluindo-se também aí a integração com outras áreas funcionais tais como Marketing, Compras, Finanças, Logística, etc.
Contudo, precisamos considerar que a padronização e utilização destes desenhos de componentes e processos similares, pode sofrer na medida em que as equipes envolvidas se tornam muito autônomas. Muitas vezes, nas organizações que combinam estruturas funcionais e por projetos, os engenheiros se vêem em situação complicada, pois não sabem se devem responder as suas áreas funcionais ou aos líderes do projeto ao qual estão alocados temporariamente. Este é um dos grandes paradigmas do gerenciamento de projetos.
Segundo Jeff Liker em sua conhecida publicação “The Toyota Way”, os princípios básicos utilizados no sistema Toyota de Desenvolvimento de Produtos podem ser agrupados em três grandes grupos: Processos, Tecnologia Aplicada e suas Ferramentas e Estruturas Organizacionais e Pessoas, que ao final devem integrar todas as fases do ciclo de desenvolvimento.
Estes processos devem ser estabelecidos ou devidamente adaptados, de acordo com o valor definido pelo cliente, separando-se o que é valor agregado do que é desperdício, criando uma metodologia de desenvolvimento de produtos que seja equilibrada e utilizar-se de rigorosa padronização nos produtos, de forma a reduzir drasticamente a variabilidade nos desenhos assim como garantir flexibilidade e obtenção de resultados previsíveis.
Quanto à tecnologia e suas ferramentas, recomenda-se adotar preferencialmente tecnologias conhecidas e que sirvam diretamente as pessoas e processos existentes, alinhando sua organização através de comunicação visual simples, além de utilizar poderosas ferramentas de padronização e aprendizado organizacional.
No que tange às pessoas e à organização, deve-se desenvolver um sistema que integre o ciclo de desenvolvimento do começo ao fim, fortalecendo a figura do engenheiro-chefe (Shusa), organizando a estrutura de forma a balancear a experiência e integração funcional matricial, desenvolver a competência técnica em todas as áreas da engenharia, construir uma base de conhecimento e aprendizado, assim como consolidar uma cultura organizacional que suporte a busca da excelência e a melhoria contínua.
Podemos ainda agrupar algumas das práticas gerenciais da Toyota em mecanismos organizacionais que quando isolados não surtem muito efeito, mas juntos dão estabilidade a um sistema que tem alcance multifuncional através de estruturas matriciais de gestão, enquanto consegue ainda sustentar a experiência requerida das áreas funcionais:
• Processos estruturais e sociais: ajuste comum ou mútuo, supervisão próxima e assistida, liderança integrativa feita pelos que detém maior conhecimento do produto.
• Processos de padronização: habilidades padrão, processos de trabalho padronizados, padronização de desenhos.
Isto posto em funcionamento faz com que a Toyota combine sistemas altamente formalizados com pitadas de gerenciamento pessoal, principalmente por parte dos Engenheiros-Chefe ( Shusa ) que asseguram que cada projeto seja flexível o suficiente para se beneficiar do conhecimento de outros projetos similares. Isto é muito comum na filosofia Toyota e gera tremenda redução no ciclo de desenvolvimento de sistemas similares entre diferentes plataformas.
A Documentação Escrita e o Processo de Decisão nos Projetos
O papel que o processo de registro e utilização do aprendizado entre projetos tem na cultura lean da Toyota é de fundamental importância para o fluxo contínuo das informações que contribuem decisivamente para sucesso nos projetos. Esta sistemática utilizada em muitas áreas da empresa proliferou-se rapidamente também entre muitos dos fornecedores diretos e tornou-se prática comum em vários deles. O objetivo principal é relatar um problema e sua solução, utilizando-se para isto preferencialmente da sistemática do PDCA, mostrada principalmente através de relatórios A3, ( nome dado ao formato do papel que equivale a aprox. 11x17 pol. ). Pode-se também gerar estes relatórios para diversas situações de “Gemba”, após um lançamento de produto e registrar suas lições aprendidas, para contar uma história importante de um projeto ou iniciativa qualquer que mereça ser aprendida por outros, ou mesmo para abordar qualquer outro assunto que seja de interesse comum. A lógica da montagem do relatório deve fazer com que haja fluidez e a história retratada flua naturalmente no documento. Muitos dos executivos japoneses e principalmente na Toyota dão preferência a este tipo de informação durante importantes reuniões com objetivo de agilizar o seu próprio tempo e o processo de tomada de decisão. Também, durante grandes etapas que definem o avançamento ou não de projetos para etapas seguintes (Project Management Gates), muitos dos Engenheiros-Chefe e outros importantes executivos preferem examinar o status atual do assunto através de relatórios A3, por vezes sumarizados e montados em painéis volantes, uma vez que certos executivos como já dito, dispõem de tempo limitado para extensas reuniões.
Estes relatórios devem ser preparados de maneira cuidadosa e eficaz, preferencialmente sendo ilustrados com fotos, sketches, gráficos e outros recursos de fácil visualização e memorização. Caso necessário, pode-se também arquivar o documento em uma pasta tamanho padrão, que estará facilmente à disposição para consultas posteriores. Desta forma, garante-se que o conhecimento acumulado seja retido, mesmo que haja a dissolução posterior do time que trabalhou naquele assunto especifico. Por isso, na Toyota e em certos fornecedores onde o processo já se encontra bastante desenvolvido, criou-se a cultura na qual ler estes relatórios é bastante valorizado pela organização e essencial para se trabalhar de forma eficaz.
A Importância das Reuniões e o Papel do Consenso no Processo de Decisão
Além do relatório escrito, uma das formas mais efetivas e poderosas de se coordenar os esforços daqueles que participam do processo em outras funções é falar-lhes cara a cara. Desta forma, cada um dos interlocutores pode entender os pontos de vista colocados e se chegar rapidamente ao consenso. Consenso é fundamental e fruto de muita discussão prévia. Este entendimento mútuo, muitas vezes toma a forma de uma reunião, mas o encontro inicial será benéfico para ambas as partes chegarem ao consenso durante a reunião formal. Este principio do “Nemawashi” também é bastante utilizado e esta intimamente relacionado à filosofia Lean de Desenvolvimento de Produtos. Um exemplo concreto seria um engenheiro de produtos e outro da manufatura que se reúnem para discutir os efeitos de determinada mudança no desenho de um produto e alinham-se quanto a sua solução (obtêm consenso) antes de se reunirem com seus superiores. De fato, muitos gerentes, executivos e demais stakeholders de projetos diversos afirmam que o contato direto é uma das formas mais efetivas de comunicação a se utilizar no desenvolvimento de produtos e projetos complexos. Isto também se confirma pela técnica do “co-location”, em que se juntam times completos ou partes do grupo no mesmo local físico. Muitos escritórios de projeto e mesmo times de determinado programa utilizam-se hoje deste recurso, chegando-se ao extremo de deslocar-se até camas para se dormir entre sessões de trabalho, mas isto que se saiba somente ocorre em casos muito especiais...
De toda forma, reuniões custosas em termos de tempo e questionáveis na eficiência e nos resultados ainda são largamente utilizadas pela maioria das empresas. Estas reuniões geralmente envolvem e agregam limitado valor se não forem adequadamente planejadas e lideradas, perdendo-se facilmente o foco do assunto principal, o que faz com que se arrastem para a zona da improdutividade. Muitos dos engenheiros envolvidos em projetos multifuncionais não possuem sequer tempo suficiente para se dedicar ao que realmente agrega valor ao desenvolvimento tendo em vista o foco nas atividades dos clientes, tal a quantidade de reuniões internas que têm de atender. Isto é uma perda de tempo e esta em desacordo com os princípios do “lean development”.
A correta preparação para a reunião, com distribuição da agenda prévia e do ponto a ser focado é fundamental para que se obtenha produtividade e o sucesso esperado. Neste aspecto, deve-se utilizar somente do tempo disponível para discutir a agenda previamente distribuída. Em reuniões com a Toyota, quando surge uma questão que requer a coordenação multifuncional, o protocolo deve ser a execução de um pequeno sumário (que preferivelmente deverá posteriormente ser retratado em um A3), apresentando a descrição do problema ou assunto em discussão, informações chave sobre o assunto, diagnóstico e recomendações para solução bem como a quem devera ser distribuído. Usualmente, se o assunto for de muita importância, o relatório é acompanhado de uma breve ligação telefônica, ou mesmo uma rápida reunião para realçar os pontos mais importantes. Espera-se do receptor da informação um feedback após a discussão com os envolvidos no assunto. Após esta fase, mais uma ou duas interações geralmente ocorrem para se chegar ao consenso e definir as ações necessárias para a solução definitiva do problema. A expectativa é entender os detalhes da causa-raiz que pode ser levantada através de técnicas diversas entre elas 5 Why, Diagramas de Ishikawa, K.Tregoe, entre outros processos de gestão e resolução de problemas.
Nestas reuniões, os participantes geralmente já conhecem os detalhes do problema e estão todos trabalhando com a mesma base de dados, além de evidentemente ter propostas para a solução do mesmo. Geralmente foca-se somente em um problema específico e sua solução, preferencialmente definitiva. Desta forma, prefere-se não misturar dois assuntos distintos em uma mesma reunião de trabalho e caso o problema não se encerre, continuar-se com a sistemática até sua resolução comprovada.
Mentores no Processo de Aprendizado
A cultura estabelecida na organização Toyota define claramente o importante papel que tem os supervisores no processo de aprendizado, gerando e retendo o conhecimento adquirido ao longo do desenvolvimento de projetos. Assim como executivos mais graduados, os supervisores estão profundamente envolvidos nos detalhes de como desenvolver desenhos de produtos. De fato, jovens engenheiros (geralmente com menos de 10 anos de experiência em desenho é o padrão na Toyota), devem necessariamente obter aprovação de seus chefes não somente quando propõem novas idéias, mas ao longo de todo processo de aprovação do desenho final do produto. Isto visa a interação continua entre eles para facilitar o processo de aprendizado dos mais jovens. Adicionalmente, tal qual os supervisores no chão de fábrica, muitos dos gerentes na área de desenvolvimento de produtos são também engenheiros que põem a mão-na-massa e efetivamente realizam o trabalho ao invés de somente administrar processos e tarefas que não agregam muito valor, mas ainda assim são necessárias. Eles aguçam suas habilidades nos produtos e adquirem conhecimento profundo nas tecnologias associadas aos produtos e sistemas em desenvolvimento. Além disso, mantem sua rede de contatos bastante ativa e continuamente renovada. Através deste processo, novas oportunidades de aperfeiçoamento dos produtos surgem, fruto de suas habilidades técnicas adquiridas e criatividade continuamente renovada. Em contraste, sabemos que muitos dos Engenheiros que se tornam Gerentes, ou mesmo Diretores aqui no Brasil, sequer se dão ao trabalho de sair de suas cadeiras para atividades de “Genchi-Genbutsu” (ver e aprender no local). Outra característica é que raramente se vê um superior dar diretamente a resposta a uma pergunta de seu pupilo; normalmente ele o faz com uma outra pergunta em cima do mesmo assunto.
Estrutura e Metodologia de Desenvolvimento voltada para o Conhecimento
A crença de que na maioria das empresas japonesas se realiza a rotação das funções com regularidade simplesmente não se aplica à Toyota. Ela tem convicção que a profunda especialização nas áreas de engenharia é essencial para suportar seu sistema de desenvolvimento de produtos.
Um engenheiro para sistemas de bancos por exemplo, trabalha com o departamento de estilo para determinar quais as melhores alternativas e conceitos possíveis antes de iniciar o desenvolvimento de desenhos em conjunto com o grupo da manufatura e fornecedores dos componentes, sendo que estes são envolvidos logo nas etapas iniciais do ciclo. As técnicas de DFA (design for assembly) e DFM (design for manufacturing) também fazem parte da rotina do desenvolvimento e favorecem a integração dos sistemas com a manufatura, tornando o processo lean do inicio das idéias até a entrega à fabricação.
A contínua renovação e disponibilidade de um banco de dados com padrões de desenho, especificações de produto e outras ferramentas úteis também tem papel fundamental e ajuda muito aos que projetam os produtos, fazendo com que estes não tenham de reinventar processos já existentes a cada novo projeto. Na Toyota, desenvolvimento de produtos e criação de padrões de desenvolvimento comuns são consideradas tarefas inseparáveis. Por isso, quando um Engenheiro apreende algo de novo, o conhecimento é imediatamente incorporado ao banco de dados e aplicado em todos os projetos da companhia, desde que aplicável, naturalmente. Isto faz com que haja a retenção e rápido fluxo do conhecimento pela organização, com a quase imediata aplicação em outros projetos. Por isso, considera-se que esta rotina é um dos importantes pilares do processo de desenvolvimento lean de produtos.
Vejamos um exemplo prático: um Engenheiro responsável por Painéis de Porta, por exemplo, pode se beneficiar das especificações existentes de tamanho e componentes de portas e começar o desenho ou imagem virtual de um novo painel a ser criado, sem ter de coordenar diretamente suas atividades com demais colegas trabalhando nos demais componentes da porta. Como resultado, o ciclo de trabalho realizado em paralelo, propicia um menor tempo de desenvolvimento e conseqüente lançamento destas inovações ao mercado.
Implicações para outras indústrias
Apesar da Toyota ser referência mundial em muitas de suas práticas, pode ser que muitas delas não sejam automaticamente aplicáveis a certas indústrias, ou mesmo companhias dentro do próprio setor automotivo. Isto deve ser mencionado, pois diferentes culturas e circunstâncias podem significar que sistemas específicos de desenvolvimento devam ser aplicados para atender às suas necessidades peculiares.
Apesar disso, podemos dizer que várias das lições aprendidas do sistema Toyota possuem boa aplicabilidade, levando-se em conta certos aspectos importantes.
Os processos de Desenvolvimento de Produto e novas idéias relacionadas devem ser integrados e implementados como sistemas coerentes, interligando as melhores práticas dentro da estrutura já existente. A Toyota obteve sucesso nesta iniciativa pois soube desenvolver e aperfeiçoar seu sistema através de décadas a fio, de acordo com sua cultura e DNA. Isto aconteceu quase que naturalmente, porém através de uma metodologia aperfeiçoada pelos seus colaboradores e fornecedores de forma contínua e consistente, utilizando-se das lições aprendidas e conhecimento gerado e retido. Empresas que porventura tomem iniciativa nesta área, mas concluam que estão no caminho errado, deverão talvez repensar suas estratégias para redesenhar sistemas e metodologias integradas tal como citado ao longo do artigo.
Sistemas e metodologias bem desenvolvidos devem levar em conta e balancear as demandas internas da experiência funcional requerida com a coordenação através destas funções ao longo dos Projetos. Tipicamente isto requer uma estrutura organizacional do tipo matricial, de preferência voltada para a gestão de projetos, com grande liderança e autonomia destes gestores. Contudo, sabemos que alcançar este estágio não é algo tão simples assim e requer alto grau de maturidade em projetos. Além disso, as práticas da Toyota nas áreas de comunicação escrita, sistematização e padronização de desenhos e atividades correlatas, bem como do poder dado aos engenheiros-chefe conforme descrito ao longo do artigo, nos dão uma boa pista de como estruturar o processo em diversas empresas e culturas distintas.
Por último, levar sempre em consideração que no final das contas são as pessoas que fazem as coisas acontecer. Na Toyota, assim como em diversas outras organizações, o sucesso no processo de desenvolvimento de produtos esta baseado na capacidade direta das pessoas envolvidas: competência técnica, experiência prática adquirida ao longo dos anos, engenheiros e gerentes que realmente põem a mão na massa, porém sem deixar de considerar o sistema como um todo, é o que faz a diferença. Este rol de atributos principais faz com que exista boa chance de sucesso no processo de integração mencionado anteriormente. Quando olhamos para o exemplo da Toyota, podemos observar dois fatores chave para que isto ocorra: Engenheiros-chefe extremamente competentes que se utilizam sabiamente de seu conhecimento para obter o respeito e a liderança requeridos, assim como bons chefes funcionais utilizando-se do bom senso e experiência para reduzir a burocracia na comunicação desnecessária, excesso de supervisão e outros tipos de confusão que eventualmente são causadas pelos processos. A ordem é simplificar sempre que possível, de forma consistente e através do aprendizado contínuo que deve ser repassado a todos e girar pela organização de forma ágil.
Referências Bibliográficas:
Liker, Jeffrey. The Toyota Way, Mc Graw Hill, 2004.
Sobek II, D, Liker, J e Ward, Allen. “Another look at how Toyota integrates Product Development”. Harvard Business Review. Agosto, 1998.
Toyota Traditions. Workbook Toyota Motor Sales USA, Inc, 2001.