Toda empresa busca crescer. Entretanto, a crescente participação no mercado traz o desafio de sustentar o aumento da produção com os equipamentos já existentes. Uma grande empresa do setor farmacêutico recentemente se deparou com esse desafio e buscou a filosofia lean para superá-lo e ampliar sua capacidade produtiva, o que dependia do aumento no grau de eficiência da entrega correta e no tempo certo de uma ampla variedade de materiais e insumos em determinados pontos da produção com espaços limitados. Ou seja, o grau de dificuldade logística aumentaria em breve.
A situação se apresentava como um problema característico de viabilizar os conhecidos Seven Rights (os sete certos) na logística de abastecimento interno: entregar o material certo, no lugar certo, no tempo certo, com o custo certo, na qualidade certa, na quantidade certa e para a pessoa certa.
Adicionalmente, o desafio incorporava diversas restrições impostas por legislação internacional e nacional na ocupação dos espaços e manipulação dos materiais e insumos no interior da área de produção e armazenagem, típicos de uma indústria farmacêutica de alto padrão de qualidade.
Uma abordagem inicial dos gestores apontava para investimentos em automação na logística com impactos negativos sobre a rentabilidade e exigindo na prática a readequação em grande monta da fábrica. A experiência da empresa na aplicação do lean em produção abriu caminho para buscar uma solução mais simples ao aprofundar os conhecimentos da filosofia agora em uma aplicação mais específica e dirigida ao problema logístico interno.
O conceito da logística lean foi aplicado de acordo com a necessidade situacional do problema e seu diagnóstico. Envolveu a prática do just-in-time interno por meio da ferramenta do milk-run interno. Os passos da sua implantação ocorreram com forte interação das equipes internas, levando à construção de um roadmap na implantação, cuja conclusão alcançou os resultados esperados e a agregação do conceito lean aos tradicionais seven rights: atendimento e execução logística com o método e ferramenta do tamanho certo, sintetizado na expressão Right Size Tool, elemento que James Womack já apresentava em seus escritos da década de 90 no livro “A Mentalidade Enxuta nas Empresas”.
Milk-run
O milk-run permite que entregas em pontos certos sejam controladas e realizadas em intervalos regulares, funcionando como uma esteira virtual que leva a cada ponto de uso o material necessário na cadência do takt-time. Não há entrega de material além do necessário, apenas aquele demandado em ciclos curtos de produção, de uma hora, por exemplo.
Entendendo o problema
Em 2017, a empresa tinha a necessidade de buscar a excelência operacional para lidar com o problema de crescimento que estava enfrentando, porém sem lançar mão de grandes investimentos e sem prejudicar a escalada com interrupções para mudanças. Um típico desafio para ser tratado com a abordagem lean: fazer mais, com poucos recursos, respeitando as pessoas e considerando seus conhecimentos.
O primeiro passo foi a realização de um mapa de fluxo de valor, que revelou a causa raiz do problema para aumento da capacidade: a falta de conexões entre os fluxos. Havia uma concepção de empurrar lotes entre as operações através das entregas logísticas de materiais e insumos em contentores de grande porte, o que piorava a situação na medida em que os espaços e os tempos eram tomados com grandes movimentações.

Figura 1: Mapeamento do Estado Atual
Mapeamento do Fluxo de Valor
Diagrama simples de todas as etapas envolvidas nos fluxos de material e informação,
necessárias para atender aos clientes, desde o pedido à entrega.
Na sequência, foi elaborado um desdobramento de ações a partir do diagnóstico e considerando o norte verdadeiro que a empresa havia estabelecido para seu crescimento, além das metas de rentabilidade. Os gestores e líderes se reuniram e elaboraram um conjunto de três A3 filhos para o A3 mãe da logística.
A3
Prática pioneira da Toyota na qual o problema, a análise, as ações corretivas e o plano de ação são escritos em uma única folha de papel (tamanho A3), normalmente utilizando-se gráficos e figuras. Na Toyota, os relatórios A3 evoluíram até se tornarem um método padrão para resolução de problemas, relatório de status e exercícios de planejamento, como o mapeamento do fluxo de valor. A3 é o termo internacional para uma folha de papel com 297 milímetros de largura e 420 milímetros de comprimento.
Esse conjunto de relatórios e as práticas intrínsecas em seu desenvolvimento levaram a empresa a planejar, de maneira mais certeira, seus passos para resolução de seus problemas e, na sequência, a desdobrá-los utilizando o conceito do hoshin kanri. O A3 do abastecimento interno teve o papel de ser o início da transformação e conectar os fluxos do outbound e inbound a partir do fluxo contínuo de produção que necessitava ser atendido.
Hoshin Kanri
Processo de gestão que alinha, tanto vertical quanto horizontalmente, as funções e atividades de uma empresa aos seus objetivos estratégicos. É desenvolvido um plano específico, geralmente anual, com objetivos, ações, prazos, responsabilidades e indicadores precisos.
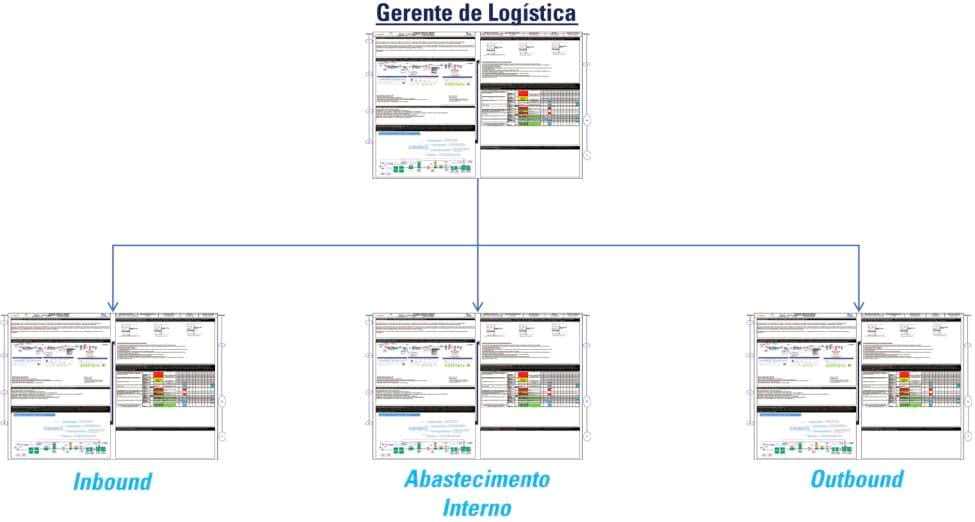
Figura 2: Conjunto de A3 na operação logística
Os objetivos principais estabelecidos eram aumentar, ao longo de 2018, a capacidade em 30%, garantindo o aumento de demanda e crescimento sem grandes investimentos e diminuindo o inventário de materiais em 20%.
Revisando os conceitos da Logística Interna Lean
Primeiramente, o conceito de fluxo contínuo é central na construção de uma logística interna sem desperdícios e com atendimento dos padrões. Na logística, esse conceito se realiza na prática do just-in-time, por meio da entrega do material necessário apenas quando for necessário. No abastecimento interno, uma das ferramentas para sua realização com alto grau de precisão é o milk-run.
A união desse conceito de entregas com a demanda de produção possibilita a construção de uma rede de fluxos. Pode-se fazer uma analogia com uma bacia hidrográfica de um rio com seus afluentes, sem represamentos e com fluxo contínuo entre suas junções. Esse percurso é realizado por meio do milk-run, uma movimentação contínua de um conjunto de carrinhos rebocados em intervalos regulares.
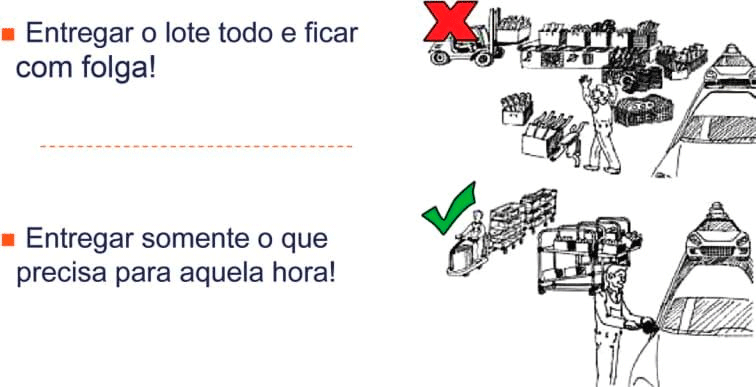
Figura 3: Mudança do pensamento básico
O milk-run permite que entregas em pontos certos sejam controladas e realizadas em intervalos regulares, funcionando como uma esteira virtual, que leva a cada ponto de uso o material necessário na cadência do takt-time. Não há entrega de material além do necessário, apenas aquele demandado em ciclos curtos de produção, de uma hora, por exemplo.
A entrega é realizada com trabalho padronizado do abastecedor, que percorre continuamente uma rota pré-definida, paradas padronizadas de carga e descarga dos carrinhos, movimentos e contentores planejados. Qualquer atraso ou adiantamento no ciclo produtivo e de entrega será rapidamente percebido. Funciona como um poka-yoke do fluxo, que alerta sobre qualquer anomalia em relação ao planejado. Dessa forma, não há excedentes de materiais, o que potencialmente esconderia as falhas ocorridas. A meta é obter uma sincronização entre entregas e produção.
O trabalho padronizado alcança também as atividades nos armazéns e movimentações em geral. Embalagens são pré-definidas e endereços de armazenagem são estabelecidos para agilizar o carregamento dos carrinhos. Os pontos de descarga também são acoplados com o trabalho padronizado dos operadores das máquinas automatizadas que conhecem e acompanham o horário de abastecimento dos materiais em intervalos regulares, apoiados por uma gestão visual que indica a programação de produção do dia, detalhada hora a hora.
Todos formam uma equipe sincronizada que sabe exatamente o que irá acontecer. E caso alguma anomalia ocorra, um atraso da entrega, por exemplo, rapidamente todos sabem do ocorrido, e a cadeia de ajuda é acionada antes de haver impacto na produção. A anomalia é estudada e tratada para não mais ocorrer. Investiga-se a causa raiz e assim se segue rumo à perfeição dos seven rights.
O cumprimento rigoroso dos horários e da qualidade da entrega vão sendo alcançados na medida em que se aperfeiçoa o trabalho padronizado de toda a equipe e sua sincronização nos pontos de acoplamento dos fluxos, de tal modo que em dado momento da implantação, alcança-se a estabilidade necessária para incluir o sistema de puxada, cuja programação é orientada pelos níveis de supermercados também visualizados por toda equipe em quadros kanban.
Começando a transformação lean
As ações se iniciaram, então, pela conexão e sincronização da produção com a logística interna, linha por linha de fabricação, por meio do milk-run e do estabelecimento de supermercados no interior dos almoxarifados de entrada e saída. Cada rota de milk-run foi projetada para entrega de todos os materiais e insumos em cada ponto de uso dos equipamentos no intervalo de uma hora.
Assim, os operadores recebiam em carrinhos o material já pronto para alimentar as máquinas, sem necessidade de manipulação de caixas de papelão. Recebiam em contentores retornáveis com a quantidade exata para produção horária. Bastava ao operador retirar do carrinho o contentor padronizado e carregar os alimentadores automatizados dos equipamentos. O operador logístico, por sua vez, levava os carrinhos carregados na viagem de ida alocando-os em cada parada e recolhendo os contentores vazios para viagem de volta. As rotas foram conectadas aos supermercados anteriores com o inbound dos materiais e aos posteriores com o outbound da expedição.
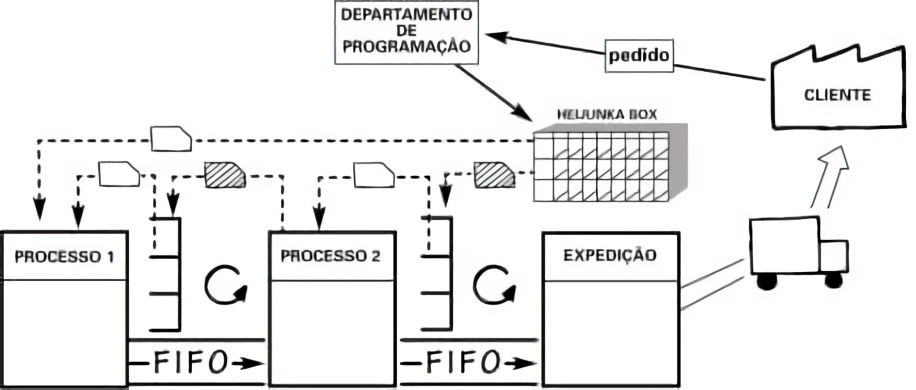
Figura 4: Fluxo contínuo de materiais e informações
Essa implantação se realizou no período de maio a outubro de 2017 por meio de um conjunto de ações encadeadas e previstas no A3 do abastecimento interno, realizadas mensalmente na forma de aprendizados on-the-job com entregas estabelecidas nos planos de ações de cada etapa:
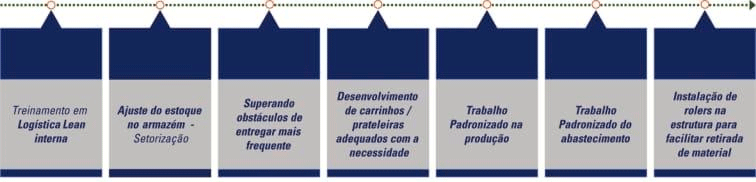
Figura 5: Plano de ação
Em novembro de 2017, a primeira rota milk-run interna era devidamente acoplada com os supermercados implantados nos almoxarifados e circulou definitivamente após uma série crescente de experimentos de gradual aumento no alcance do estado futuro, na medida em que eram realizados os testes e simulações controladas desde maio de 2017.
Essa foi uma peculiar estratégia de implantação desse caso na indústria farmacêutica, cujo ineditismo de aplicação do lean em ambiente de extrema regulação de mudanças, exigiu o planejamento de testes e experimentos seguidos. Os primeiros foram realizados fora do ambiente de produção, em espaços livres para visualização do estado futuro, utilizando materiais aproximados, econômicos e de baixa fidelidade. O objetivo era estabelecer o conceito e nivelar o entendimento entre os participantes.
Na medida que tais experimentos e simulações permitiam o entendimento dos envolvidos, o grupo foi passando gradativamente para os testes parciais no ambiente de produção. Inicialmente com circulação do veículo teste na rota proposta, depois seguindo-se a experimentação de embalagens e protótipos de carrinhos, as cronometragens e, por fim, o detalhamento dos métodos e movimentações junto com operadores de produção e logística. Aperfeiçoamentos foram sendo feitos teste por teste até o atingimento da solução final.
Resultados e Conclusão
No início de 2018, os primeiros resultados da rota piloto de milk-run foram acrescidos da implantação das outras rotas de abastecimento, cujas implantações foram mais rápidas em função do aprendizado alcançado.
Em todas elas, a observação no gemba demonstrava a redução de movimentações de operadores e um maior controle do takt-time com alcance das programações planejadas. O milk-run interno funcionava como uma esteira a levar aos operadores os materiais certos no ritmo certo.
A produtividade aumentou em 22% com melhor utilização dos operadores nos intervalos de 1 hora das entregas. A movimentação, por exemplo, foi reduzida entre os pontos de uso e alimentação dos equipamentos como pode ser visualizado na comparação do gráfico espaguete.
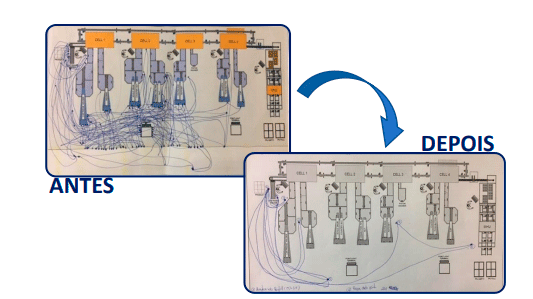
Figura 6: Comparação dos gráficos de espaguete antes e após a implantação
Por outro lado, a garantia alcançada em ter os materiais certos no tempo certo reduziu as faltas de produção, elevando o OEE dos equipamentos. De forma combinada, a maior produtividade com a melhoria da eficiência dos equipamentos permitiu atender o aumento de capacidade sem investimentos. Em termos de estoque a redução de 30% foi alcançada no estoque de produção, havendo ainda a meta de avançar nos estoques de entrada. Uma relação de outros resultados alcançados pode ser visualizada a seguir:
- 95% de manuseio de materiais removidos.
- 40% de redução do tempo de preparação da ordem de produção.
- 66% de redução de transporte de materiais.
- 97% de redução do estoque da produção.
- Zero problemas ergonômicos na produção.
- 22% de aumento da produtividade (2 operadores por turno).
Por fim, o caso permitiu um aprendizado metodológico na aplicação da logística lean em ambiente rigorosamente regulamentado em suas práticas de operação e validação de mudanças, como é o caso da indústria farmacêutica. De um lado, a prática das experimentações graduais até entendimento do estado futuro permitiu que o transplante do experimento para o ambiente definitivo se desse de forma mais assegurada e com confiança de todas partes envolvidas. De outro, o estabelecimento nestes experimentos do grau correto de padronização em ferramentas, carrinhos e métodos de abastecimento, promoveu a reflexão e incorporação do aprendizado de incluir nos consagrados seven rights da logística um oitavo elemento propiciado pela aplicação do lean: the right tool and method (o método e ferramenta certos).