Este artigo procura mostrar o papel da “Liderança” e da “Média Chefia” no dia a dia da fábrica, interagindo para estabilizar os processos produtivos com procedimentos, métodos, e ferramentas adequadas na Toyota do Brasil. Destacaremos ainda sua importância no esforço para garantir o “espírito” de união do grupo para a melhoria contínua, quais deveriam ser as suas atividades principais, e finalmente, apresentar uma sugestão para as empresas que estão em suas respectivas jornadas lean, e qual seria a sua função principal.
1) Como medir e acompanhar a estabilidade na produção
Como mostramos no artigo “Estabilidade nas áreas produtivas da Toyota”, o indicador utilizado para se medir a estabilidade é o “downtime”.
O monitoramento é feito pelo “quadro de acompanhamento dos problemas” (ver manual “Criando Fluxo Contínuo” – Mike Rother & Rick Harris, versão 1.0 de Janeiro 2002, página 86) e geralmente anotado pelo líder de grupo, sendo que o supervisor ou gerencia da área verificava durante os intervalos, e a direção (gerencia da planta) no final do dia.
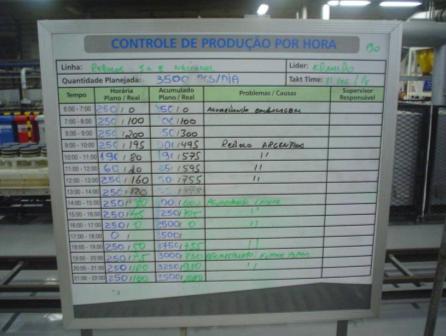
Fonte: Saint Gobain Abrasivos – Planta de Paulista (Fórum NE – 2007)
Importante lembrar que todos as anormalidades oriundas dos 4M’s que causavam direta ou indiretamente a parada da produção, eram acusados nesses quadros de acompanhamento e geravam o downtime. Assim problemas como os atrasos da linha em decorrência de absenteísmos ou operadores sem treinamento (Mão de Obra), setups elevados devido à falta de padronização (Método), peças e componentes que chegavam atrasados (Material) e máquinas que trabalhavam com problemas (Máquina) contribuíam para a instabilidade.
Não se atingindo a produção planejada (determinada pelo tempo takt), todo motivo de parada era quantificado (quanto tempo) e qualificado (o que aconteceu). A responsabilidade das pessoas (líderes de grupo) era analisar e resolver no mesmo instante os problemas observados hora a hora, e a média chefia (supervisão e a gerencia da área) e sua equipe resolvê-los o mais rápido possível com métodos adequados (ver estrutura organizacional no Léxico Lean, versão 2007, página 47). O objetivo era atingir eficiência de no mínimo 95% em relação ao planejado, em quantidades ou tempo permissível de parada.
2) O método para resolução dos problemas
Observamos que a Liderança tem papel fundamental na estabilização da produção devido a sua atitude de tornar público os problemas e resolvê-los com a maior brevidade possível, utilizando os métodos científicos: “5 Por quês” para se encontrar a causa raiz e o “5W+1H” (Why, What, When, Where, Who, e How) para se definir as ações.
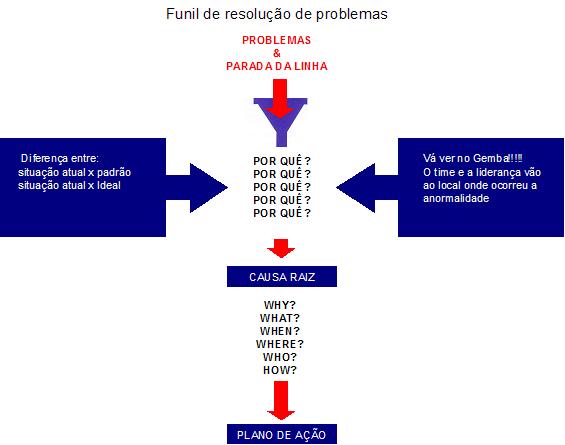
Ao se deparar com algum problema detectado no quadro de acompanhamento da produção, cabia ao líder ou supervisor iniciar a análise do problema, e em conjunto com sua equipe resolvê-lo, seja através de uma contenção ou eliminação total. Funcionários volantes de todas as áreas eram envolvidos e com a liderança deste responsável, executavam o plano traçado em pouco tempo.
Exemplo de um problema de parada da linha identificada e analisada no local:
Quando os problemas eram complicados em termos de tempo de execução ou dificuldade técnica, como mencionado no artigo anterior eram parametrizados e priorizados. Os mais importantes e significativos eram escolhidos como tema para os grupos de CCQ (círculo de controle da qualidade) ou CK (círculos de kaizen), que duravam de 3~6 meses de trabalho. Invariavelmente sempre se conseguia bons resultados, e no mínimo havia a redução do desperdício. Nessas atividades em grupo, normalmente utilizávamos o “gráfico de Ishikawa” ou “espinha de peixe”, onde todas as causas imediatas eram levantadas e direcionadas levando-se em conta os 4 M’s, Mão-de-Obra, Método, Material e Máquina, nessa ordem de prioridade.
O planejamento dos kaizens das equipes para se resolver um problema era determinado pelo documento A3 (ver “Léxico Lean”, segunda edição, versão 2.0 de Abril 2007, página 2), onde temos as etapas de Introdução e objetivos, Situação atual, Situação futura, Plano de ação, e os Indicadores e Ganhos.
Para se administrar os vários planos de ação gerados para se resolver os problemas, normalmente fazíamos 3 tipos de reuniões entre as equipes:
Diária de 5 minutos com toda a equipe de produção feita nas áreas fabris, onde se procurava informar a cada turno sobre os problemas e melhorias feitas no turno anterior.
- Semanal-1, de 1 hora de duração no máximo, com os setores do Planejamento e da Qualidade, onde eram feitos os monitoramentos das melhorias em execução e pendência.
- Semanal-2, de 1 hora de duração no máximo, com a Direção, onde eram determinadas as diretrizes principais.
Todo esse esforço procurava manter a estabilidade produtiva dentro dos padrões mundiais da empresa, e a atitude de entregar à equipe a responsabilidade para resolver os problemas (sendo orientados pela chefia), era um fator importante pois quem mais conhece o problema e sua solução são aqueles que estão diariamente enfrentando as dificuldades.
A participação dos funcionárias da área onde se originou o problema criava a “unidade da equipe”, e ao se dar a oportunidade de todos serem ouvidos e poderem participar ativamente na resolução trazia a satisfação pessoal, a melhoria da comunicação e envolvimento.
3) As atividades principais da liderança e média chefia
Abaixo mencionamos algumas das principais atividades necessárias para a “Liderança” conseguir manter a estabilidade produtiva, considerando-se os 4M’s da produção. É importante frisar que sempre quando acontecia alguma anormalidade na produção (problemas que aumentavam o downtime), de maneira imediata todos os responsáveis das áreas “fornecedoras” de componentes ou de algum tipo de “prestação de serviço interno” (por exemplo o departamento da Manutenção) compareciam ao local para auxiliar a “Liderança”. Esta “força de equipe” é o fator mais importante para se identificar os problemas, propor contra-medidas e assim sanar os mesmos para que não ocorressem mais.
a) Mão de Obra
- Formação de novas lideranças com o conhecimento necessária da filosofia lean e com a tolerância zero aos problemas.
- Implementação da multi-funcionalidade nas áreas produtivas e assim desenvolver e qualificar os funcionários.
b) Método:
- Acompanhamento do andon da produção para detectar rapidamente onde irá acontecer o problema, e assim tomar atitude “prevencionista”, para que não ocorra a parada.
- Acompanhamento do quadro de controle da produção horária para verificar o andamento da produção real e planejada, tomando-se as atitudes “corretivas necessárias”.
- Manutenção da sistemática de levantamento e resolução dos problemas, verificando e direcionando imediatamente a solução dos problemas fáceis (através dos encarregados, líderes e volantes), e planificando a ação para os mais difíceis e complexos.
- Elaboração, revisão e controle dos documentos do Trabalho Padronizado, balanceando a produção e readequando o lay-out de acordo com a mudança do Takt.
- Controle visual da mão-de-obra através do quadro kanriban (Gestão visual, um quadro de controle da presença dos funcionários, identificando os postos chaves de trabalho com relação a experiência, e da multifuncionalidade), fazendo-se as escalas de trabalho e promovendo o job-rotation.
- Manutenção e melhoria contínua da Segurança e do programa “5S”.
c) Material:
- Assegurar que os supermercados sejam abastecidos, monitorados e revisados.
- Assegurar que a rota de abastecimento esteja sendo cumprida.
- Implementação de poka-yokes para controle e contenção dos problemas de material.
- Acompanhamento das modificações de produtos e componentes, visando a revisão das embalagens e seu acondicionamento.
d) Máquina:
- Execução dos primeiros socorros em paradas de máquina.
- Planejamento e implementação da Manutenção Autônoma, através do treinamento dos funcionários e da implementação de check-lists das principais máquinas.
- Planejamento em conjunto com a Manutenção, o plano de Manutenção Preventiva e Corretiva.
- Desenvolvimento das máquinas, dispositivos e equipamentos que atendam ao Takt, em conjunto com a Engenharia.
4) Conclusão
Essas atividades acima são necessárias para se garantir a resolução dos problemas detectados na produção, e a “Liderança e Média Chefia” desempenham um papel importante nesse sistema.
O trabalho em equipe é o diferencial mais importante do Sistema Toyota de Produção quando se fala em método, ou seja, o comprometimento e o envolvimento das pessoas trabalhando em grupo para a resolução dos problemas.
Como conseguíamos a estabilidade da produção? Bastava resolver os problemas quando eles apareciam, o mais rápido possível, com o método científico ou embasado no conhecimento e atitudes da Liderança. Isto é muito difícil de encontrar nas empresas atuais, ou seja, “Lideranças” sem vaidades pessoais ou políticas com um único comprometimento: o bem estar da coletividade. Se todos cuidassem da empresa onde trabalham, como cuidam de suas casas e pertences, teríamos fábricas, corporações, cidades, estados e paises com poucos desperdícios e certa estabilidade produtiva.
Para as empresas que já estão há algum tempo na Jornada Lean e que lutam para a manutenção das ferramentas já introduzidas, a sugestão que fica é a de formação dessas lideranças sempre pelos seus superiores. Melhor explicando, a transferência de conhecimento deve vir de cima para baixo, ou seja, o Presidente deve ser profundo conhecedor da filosofia lean e “ensinar” o Diretor que deve fazer o mesmo com o Gerente e assim por diante.