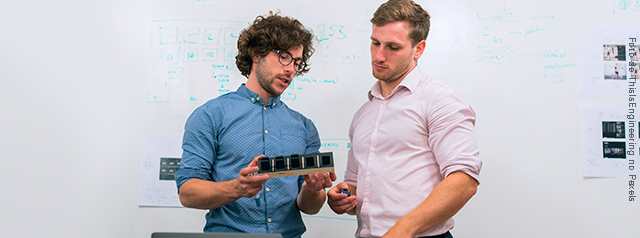
Cada vez mais empresas buscam na filosofia lean um novo paradigma para nortear suas operações em direção a uma redução de custos de modo a torná-la competitiva. E focalizam essencialmente em seus processos de manufatura.
Em grande medida, isso deve-se ao fato de que a Toyota é mundialmente reconhecida pelo seu inovador sistema de produção (TPS-"Toyota Production System"). O que nem todos ainda perceberam é que grande parte do sucesso atribuído ao TPS tem sua origem em fases anteriores à produção em si.
O ponto de partida do "Lean Thinking" é definir o que é valor para o cliente, traduzido em produtos e/ou serviços, ou como preferimos dizer, soluções para os clientes.
A Toyota tem conseguido, sistematicamente, desenvolver produtos e respectivos processos com menores custos, mais rapidamente e com melhor qualidade do que seus concorrentes. Mas, em grande medida, este sucesso deve-se à aplicação da filosofia implícita no TPS em suas diversas atividades.
O processo de desenvolvimento dos produtos, além de ser capaz de captar as dimensões do que seria valor para o cliente, é orientado pelas implicações operacionais e tecnológicas que estarão, num momento seguinte, presentes nos processos de manufatura, dentro e fora da empresa.
O tema desenvolvimento de produtos e processos na Toyota tem sido o foco dos trabalhos de pesquisa de Allen Ward, da Universidade de Michigan.
Assim como, por anos, os reais conceitos e práticas da Toyota na manufatura ficaram escondidos ou pouco compreendidos, agora o desafio é desvendar a "caixa preta" presente nos conceitos da empresa nesta dimensão dos negócios.
Ward é doutor em engenharia mecânica pelo MIT, foi ganhador do Prêmio Shingo e teve, por duas vezes, seus papers premiados pela Design Theory and Methodology Conference, realizada pela ASME (American Society of Mechanical Engineers). Teve artigos veiculados em publicações importantes como a Sloan Management Review e a Harvard Business Review.
Ward faz uma grande contribuição ao iluminar o Conceito Lean de Desenvolvimento de Produtos e Processos, ao qual ele chama de "Aprendizado Emergente" ou o "jeito Toyota" de conceber veículos e operações.
Desperdícios
A eliminação dos desperdícios em todas as atividades da empresa, como sabemos, é um dos objetivos fundamentais da filosofia lean. Ward identifica os mais relevantes desperdícios presentes nos fluxos e atividades envolvidas especificamente com o processo de desenvolvimento:
- Dispersão
Desperdício decorrente de mudanças freqüentes no modo de se fazer as coisas. Perde-se conhecimento e know-how adquiridos ao longo do tempo. A toda hora inicia-se uma nova "curva de aprendizagem", requerendo requalificações. O problema pode se agravar à medida em que mudanças tornam-se mais constantes e abrangentes.
- "Handoffs"
Causado pela separação entre conhecimento, responsabilidade e autonomia de ação. Muitas empresas separam essas três dimensões, buscando fragmentar as atividades ao máximo, acreditando que quanto maior a divisão do trabalho, melhor. Existem gerentes que detém a responsabilidade, porém não entendem nada sobre design. Especialistas determinam os parâmetros para o design, mas não o fazem. Supervisores de engenharia aprovam as partes, mas não participam do design. Ou, o operador do CAD determina as formas mas não conhece nada de engenharia e não tem nenhum grau de responsabilidade sobre o desempenho do projeto.
- "Wishful thinking"
Desperdício decorrente da inadequação de decisões tomadas de forma precipitada, carentes de dados corretos, experimentações e questionamentos adequados. Os projetos tradicionais frequentemente tomam decisões sem base em dados, causando enormes desperdícios que vão acumulando-se ao longo do tempo. Por exemplo, as especificações iniciais de um projeto comumente impõe inúmeras restrições ao longo do ciclo de vida do projeto.
O sistema
A definição de um sistema, com cinco elementos fundamentais integrados, é uma das grandes contribuições das pesquisas de Ward, mostrado na figura abaixo:
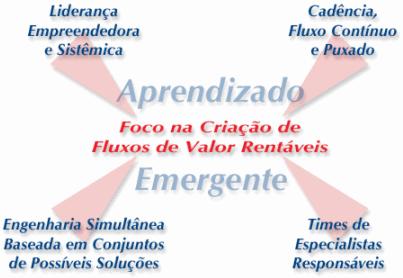
Examinaremos cada um destes elementos com mais detalhe.
1. Foco na criação de fluxos de valor rentáveis
O objetivo final de um processo de desenvolvimento lean deve ser o funcionamento pleno de um fluxo de valor rentável. Pensar o produto a ser manufaturado conjuntamente com as operações das quais resultará é fundamental para que se consiga otimizar a utilização dos recursos, evitando desperdício e garantindo a rentabilidade econômica. Os fluxos envolvidos nos processos de desenvolvimento devem estar orientados para a criação de valor para o cliente final.
2. Liderança empreendedora sistêmica
Todo o processo de desenvolvimento na Toyota possui um líder empreendedor experiente. A relevância desse líder chama a atenção, pois seu papel permeia praticamente todas as dimensões envolvidas no processo. Esse líder deve conhecer profundamente os desejos e aspirações do cliente final, deve garantir a rentabilidade do projeto, deve administrar impasses, levando a consensos, deve ser oferecer suporte técnico; enfim, deve ser capaz de nortear todo o processo de forma a garantir seu sucesso.
3. Cadência, fluxo contínuo e puxado
Assim como no chão de fábrica, o ritmo cadenciado e a lógica do fluxo contínuo e puxado também são os elementos operacionais essenciais que garantem a agilidade e os baixos custos dos processos de desenvolvimento. Deve-se garantir que a informação e o conhecimento fluam de maneira cadenciada ("takt time"), contínua (sem esperas, sem retornos) e puxada (de acordo com a demanda real da próxima etapa) durante todo o desenvolvimento. A informação certa deve estar disponível no momento certo, no lugar correto e na quantidade adequada. Lembre-se que uma das maiores fontes de desperdícios verificadas nos processo de desenvolvimento diz respeito ao uso incorreto que se faz do conhecimento e da informação gerada.
4. Times de especialistas responsáveis
Especialistas devem ser combinados de forma a comporem equipes multidisciplinares, suficientemente autônomas, co-responsáveis pelo projeto. A tarefa de criar novos conhecimentos, sistematizá-los e comunicá-los ao resto das pessoas envolvidas no projeto fica a critério dos times de especialistas responsáveis. São esses especialistas os responsáveis pela transposição de barreiras tecnológicas e de conhecimento envolvidas na busca de fluxos de valor enxutos e rentáveis. A visão sistêmica de otimização do todo e não das partes é fundamental.
5. Engenharia simultânea baseada em conjuntos de possíveis soluções
Os designers da Toyota pensam em termos de conjunto de possíveis alternativas num primeiro momento, e, à medida que a data limite para o lançamento do produto se aproxima, esse conjunto de alternativas vai sendo reduzido. As possíveis soluções vão se afunilando. O que se mostra inviável é descartado e o que resta continua a ser estudado. O resultado final, portanto, não fica sujeito a mudanças. A solução é definitiva.
Algumas decisões são propositadamente retardadas, por mais paradoxal que isso possa parecer, pois se tomadas no início do processo e de forma equivocada podem vir a invalidar grande parte do trabalho a ser feito dali em diante. Atrasos dessa natureza podem comprometer o timing de lançamento e inviabilizar o projeto como um todo.
Informações mesmo incompletas, não definitivas e antecipadas são passadas para os fornecedores, que seguem o mesmo método: apresentam uma gama de soluções e, junto com a montadora, vão descartando as alternativas que se mostram menos viáveis. A relação da Toyota com seus fornecedores é bastante peculiar com parcerias efetivas, e usa a sua cadeia de fornecedores como fonte de conhecimento e melhoria de competitividade.
Para que conceber o produto nos mínimos detalhes sem considerar as restrições a que estarão sujeita a manufatura desse produto? É por isso que não se caminha no desenvolvimento do produto sem se ter a certeza de que aquilo que ali se está concebendo é plenamente viável dentro de um conjunto de restrições operacionais muito claras a todos.
Sumarizando
O "Aprendizado Emergente" está implícito nessa dinâmica pois trata-se de saber gerir o conhecimento acumulado com as experiências, ao longo do tempo. Não se reinventa a roda a cada novo projeto. Dá-se enorme importância às lições aprendidas, que não se perdem.
Esse conhecimento acumulado não fica restrito a documentos formais ou rotinas sistematizadas apenas, mas se concentra também sob a forma de experiências pessoais daqueles ligados ao projeto. São essas pessoas, trabalhando sob supervisão de uma "liderança empreendedora", inseridas num processo de comunicação eficiente e direto e sob a forma de equipes multidisciplinares, que tornam factível o excepcional desempenho verificado.
O Desenvolvimento Lean de Produtos está totalmente alinhado com a filosofia lean e com as práticas adotadas na empresa, quer sejam na fábrica, na relação com clientes e fornecedores e na organização das ações internas e gestão dos fluxos de valor.
Bibliografia
Os artigos publicados por Allen Ward são:
"The Second Toyota Paradox: How Delaying Decisions Can Make Better Cars Faster", Sloan Management Review, Primavera 1995, v 36, p. 46-61.
"Toyota's Principles of Set-Based Concurrent Engineering", Sloan Management Review, Inverno 1999, v 40, p. 67-83.
"Another Look at How Toyota Integrates Product Development", Harvard Business Review v 76, n 4, Julho-Aug.,1998, p. 36-50.
Outros livros interessantes sobre o assunto são:
Womack, James; Jones, Daniel e Roos, Daniel. "A Máquina que mudou o mundo". Editora Campus, R.J., 1992. Ver em particular o capítulo 5.
Clark, Kim e Fujimoto, Takahiro. Product Development Performance. Harvard University Press, 1990.
Fujomoto, Takahiro. The Evolution of a Manufacturing System at Toyota. Oxford University Press, New York, 1999.