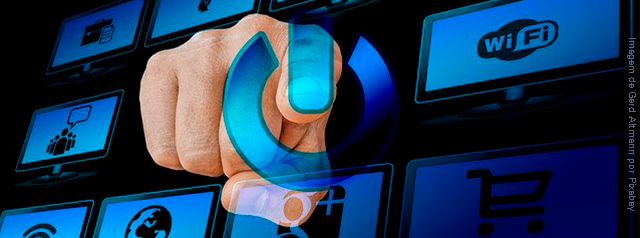
O nível de automação ideal para sistemas enxutos
Autor: Rick Harris
Publicado em "Lean Directions", um jornal eletrônico elaborado pela Society of Manufacturing Engineers.
Por alguma razão, as pessoas assimilaram a idéia de que sistemas lean requerem operações manuais, cabendo aos operadores as tarefas de abastecer as máquinas, operar o ciclo, retirar a peça e passá-la adiante. Porém, isto é um grande engano. Atingir uma fluidez eficiente no "processo puxador" do fluxo de valor, elemento indispensável para uma bem sucedida conversão lean, é praticamente impossível sem um certo nível mínimo de automação.
O "truque" está em determinar o nível ideal de automação. Pouca automação pode representar perda de eficiência. E automação demais pode significar queda na confiabilidade e menor domínio sobre o sistema. O nível certo é aquele em que a manutenção não consome recursos injustificáveis. Isso pode facilitar suas decisões e permitir que 95 a 100% de tempo de utilização requerido pelo processo puxador possa ser atingido.
Nível de automação
N
í
v
e
l
|
|
Carga da
máquina |
Ciclo da
máquina |
Descarga da
máquina |
Transferência de
peças |
1 |
|
|
|
|
2 |
|
Auto |
|
|
3 |
|
Auto |
Auto |
|
A grande divisão |
4 |
Auto |
Auto |
Auto |
|
5 |
Auto |
Auto |
Auto |
Auto |
Dentro das cinco possibilidades relacionadas a níveis de automação, você poderá contar com essa confiabilidade sólida posicionando-se próximo daquilo que nós, do Lean Enterprise Institute, chamamos de Automação em 3º Nível (veja figura). Esse Nível fornece a mais eficiente e flexível combinação entre os movimentos do operador e dos materiais. Entenda porquê.
Primeiramente, você precisa compreender que o "processo puxador" deve obedecer a uma mecânica semelhante a de um jogador de futebol que nunca se machuca, nunca é expulso de um jogo. Ou seja, está presente em todos os jogos.
A razão para isso é que o "processo puxador" é o seu referencial de programação. Geralmente é onde se inicia a implementação do Estado Futuro, mais enxuto, esboçado a partir do Mapeamento do Fluxo de Valor. O "processo puxador" geralmente se encontra ao final do fluxo de valor, onde os produtos tomam a sua forma definitiva. Na maioria das vezes é o processo final de todo o fluxo de valor, mas há exceções.
O processo é chamado "puxador" pois a cadência com que os materiais fluem através dele é que determina o ritmo ao qual as operações anteriores no fluxo de valor devem obedecer. A acuracidade com que transcorrem essa operações determinantes de ritmo define a forma como se atende à demanda do cliente final. Disfunções no "processo puxador" comprometem todo o fluxo de valor, que jamais será lean de fato. Serão necessários mais pessoas, equipamentos e materiais para atender à demanda.
Explorando os Níveis de Automação
Com o Nível de Automação 1, o operador é quem abastece a máquina, opera o ciclo, retira a peça e transfere-a para a estação de trabalho subsequente. Os problemas, nesse caso, são os elevados custos e a qualidade, que fazem deste um Nível impraticável. Ciclos automáticos são necessários para garantir padrões mínimos de qualidade; além do mais, ciclos manuais são demasiadamente caros em algumas regiões, devido aos elevados custos da mão-de-obra.
O Nível 2 já representa alguma melhoria. Os operadores abastecem a máquina, cujo ciclo agora é automático, retiram manualmente a peça pronta e a transferem, também manualmente, para o processo seguinte. Mas existem sérios empecilhos. O operador chegará ao processo seguinte carregando a peça que acabara de retirar da primeira máquina. O operador terá que colocar a peça em algum lugar, retirar a peça pronta dessa segunda máquina, abastecer a segunda máquina com a peça ainda por ser processada para só então executar o ciclo. Então, o operador do processo seguinte terá que proceder dessa mesma forma, repetindo esses esforços desperdiçados.
O problema mais óbvio remete ao fato de o operador manusear mais de uma peça em estágios diferentes de produção: tanto aquela que ainda não passou por determinado processo, quanto a peça pronta para seguir para a operação seguinte. Algumas vezes, os gerentes imaginam conseguir eliminar esse desperdício colocando as peças já processadas em containers ou racks. Na verdade, o desperdício não é eliminado e o problema persiste sem solução. O duplo manuseio é convertido em maior carga de trabalho para dois ou mais operadores e em estoques entre os processos que daí resultarão.
Já o Nível 3 consegue otimizar o fluxo através do "processo puxador" fazendo uso da automação para que as peças possam ser ejetadas automaticamente uma vez finalizado o ciclo. Com isso a máquina estará sempre vazia quando itens provenientes de operações anteriores chegarem até ela. O descarregamento automático eliminará aproximadamente 50% do manuseio necessário. Além do mais, as máquinas podem ser menores, mais eficientes e menos complexas quando empregado o Nível 3, o que requer menos recursos para manutenção e suporte técnico.
Outro benefício: sistemas de descarregamento automáticos não são complicados de se projetar (se comparado a sistemas onde o abastecimento também é automático), o que torna o Nível 3 relativamente barato. É a melhor estratégia de investimento, pois o operador abastece a máquina, a máquina opera o ciclo e ejeta a peça automaticamente. Quando o operador chega com o próximo item, basta abastecer a posição vazia, acionar a máquina, pegar o item processado e transferi-lo à operação seguinte.
Com o Nível 4 de automação, deixa-se a simplicidade, a confiabilidade e os baixos custos do Nível 3 para trás e passa-se a lidar com maior complexidade, tempo desperdiçado e elevadas despesas. A máquina é carregada e descarregada automaticamente. O operador ainda transfere manualmente os itens para a operação seguinte. O problema com este Nível é que o abastecimento automático requer sensores ou "sistemas de visão" para posicionar corretamente o item. O operador é geralmente mais eficiente, já que é capaz de fazer os ajustes de imediato ao alimentar a máquina.
A complexidade extra que começa a aparecer com a utilização do Nível 4 torna-se mais problemática quando é empregado o Nível 5, em que todo o processo é automatizado. A confiabilidade de um "processo puxador" com este grau de automação beira 70% ou menos. Imagine as implicações disso para o resto das operações e, consequentemente, para o cliente final.
Outro problema com Níveis de Automação além do Nível 3 é que os tempos de troca podem tornar-se demasiadamente longos, graças à maior complexidade envolvida. Isso leva à necessidade de maiores turnos e estoques. E o que é pior: se a demanda ficar abaixo do previsto, você estará diante de uma situação economicamente desfavorável. Se a demanda for maior do que o esperado, sua única solução será investir, às pressas, em uma outra linha igualmente automatizada.
Com o Nível 3, por outro lado, será possível adicionar operadores para se aumentar a produtividade, ao invés de investir em novos equipamentos. Note, entretanto, que se o "takt time" for de apenas um ou dois segundo por peça, os Níveis 4 e 5 devem ser considerados como opções reais.
Não é que a automação seja um mal. Na realidade, não existe sistema lean sem o mínimo de automação. Mas temos certa cautela com relação à super-automação, sustentada pelo amor à tecnologia e pelo foco de nossos sistemas contábeis no custo direto de mão-de-obra - sem a necessária preocupação com o tempo de utilização e com a sub-utilização de capacidade instalada. Assim, um dos grandes desafios na implementação da manufatura enxuta é a correta determinação do Nível de Automação a ser empregado. O segredo é usar o Nível certo - o de 3º Nível.
Rick Harris
Ex-Gerente de manufatura da Toyota, Rick Harris é co-autor, com Mike Rother, do manual Criando Fluxo Contínuo. Ele é também presidente do Harris Lean System Inc., sediado em Kentucky, EUA).