A jornada lean da Wabtec, antiga GE Transportation, é de longa data. Muitos esforços de melhoria sempre fizeram parte da cultura da organização. Entretanto, um novo pico de demanda no ano de 2011 apresentou uma nova oportunidade à organização com a qual não era possível lidar apenas com aplicações de conceitos pontuais e em algumas áreas da empresa.
Então, um grande momento “aha” surgiu, trazendo à tona que uma transformação global precisaria ser feita para a sustentação das melhorias e para maior capacidade de atendimento com qualidade aos clientes. O elo entre as iniciativas pontuais e uma completa transformação da organização, com melhorias sustentadas e desenvolvimento das pessoas, foi o hoshin kanri. Vamos contar aqui como tudo isso aconteceu, quais foram os resultados e aprendizados adquiridos e como estamos agora após alguns anos.
Dando um passo atrás: antes de construir uma ideia, é preciso desconstruir outra
Desde o ano de 2008-2009, a GE Transportation havia construído uma cultura de trabalho em silos. Essa cultura levava as pessoas a adquirirem uma resistência em relação às mudanças e novas iniciativas.
Dado esse cenário, a empresa observou que a abordagem que vinha sendo adotada na época não era algo propício à colaboração. Por isso, a diretoria da organização entendeu que uma transformação na forma de pensar das pessoas deveria ser feita.
Essa transformação deveria ser muito bem pensada para não frustrar os colaboradores; pelo contrário, deveria trazer segurança, entendimento de que os problemas são importantes como oportunidades de melhorias e que os processos precisariam ser melhor estruturados para apoiar e melhorar o trabalho de todos, conectando os setores e trabalhando mais juntos, como uma equipe.
O aprendizado que se queria construir na mente de todos era de que o lean é sobre melhorar, trazer mais faturamento para a empresa, mais serviço, mais diversidade para o portfólio da organização e também sobre desenvolver pessoas, e isso não é possível se estamos trabalhando em silos. O que faz a diferença ao observar essas duas formas de pensar é a abordagem destrutiva (antilean) ou construtiva (verdadeiramente lean) que será utilizada no processo.
As primeiras iniciativas verdadeiramente lean
A unidade da Wabtec no Brasil (na época, GE Transportation), a princípio, apenas reformava locomotivas. Com a decisão de começar também a fabricar locomotivas, a demanda da empresa começou a crescer, até que no ano de 2011 houve um pico muito grande que forçou a empresa a fazer algo para conseguir atender e sobreviver no mercado.
Começando a transformação de forma pontual na área da manufatura, eles escolheram uma estação de trabalho e decidiram aplicar tudo que sabiam de lean ali. Erros aconteceram, ajustes foram feitos, muitos aprendizados foram adquiridos nesse processo até que um modelo operacional que fazia sentido e que trazia melhores resultados foi definido. Tudo que estava acontecendo era novo; portanto, o foco, além de operacional, também foi no desenvolvimento das pessoas.
Posta essa definição no piloto da estação de trabalho, um roadmap foi criado para orientar e replicar as melhorias para as outras estações. Essa abordagem inicial na fábrica foi estratégica para mostrar às pessoas que os resultados estavam surgindo, que isso estava tendo um efeito positivo para a empresa e para os colaboradores. Assim, grande parte da resistência instaurada foi quebrada.
Hoshin Kanri: conectando as áreas e as pessoas e consolidando as mudanças
A diretoria e a equipe de melhoria perceberam que essas mudanças iniciais eram apenas a ponta do iceberg e que havia um leque enorme de oportunidades nas áreas de operações e, posteriormente, serviços. A necessidade, então, nesse momento, era de ter uma estratégia mais robusta, conectando e engajando as outras áreas da organização e disseminando a todos a cultura e os fundamentos lean. E foi aqui que o Lean Institute Brasil embarcou nesta história, apoiando a implementação do lean na empresa, que começou a se enraizar mais profundamente em sua cultura, deixando de ser apenas pequenos projetos pontuais de melhoria com uso isolado de ferramentas.
O norte verdadeiro traçado foi de ser uma operação de classe mundial, sendo a primeira escolha para os clientes e empregados, com uma forte colaboração com os fornecedores e a comunidade. Como pontapé, dois dias de treinamento foram realizados, um dia sobre hoshin, meio dia sobre A3 e meio dia sobre liderança. Nesse momento, todo o pessoal da diretoria de supply chain, área corporativa e todos os donos dos A3 de áreas passaram a se alinhar melhor quanto aos processos da organização.
Esse treinamento aprofundou o conhecimento dos colaboradores nas ferramentas, na filosofia e na cultura lean. Com a ajuda do hoshin e o apoio ativo da liderança, um ambiente verdadeiramente lean começou a se difundir por todos os cantos.
A partir daí, a empresa precisou transpor seu norte verdadeiro para um A3 mãe estratégico, desenvolvido pela diretoria de supply chain. A construção desse A3 mãe foi uma etapa vital no processo e contou com a colaboração de todos gerentes que respondiam a essa diretoria. Em pouco tempo, o A3 se tornou o guia para o alinhamento e o desdobramento da estratégia na área.
Já que o norte verdadeiro da empresa, de ser uma operação de classe mundial, demandava a eliminação de desperdícios e uma maior agregação de valor pela perspectiva do cliente, ferramentas e atitudes lean começaram, então, a ser conectadas às estratégias desenvolvidas.
Assim se iniciou a construção dos A3 filhos, buscando o alinhamento e o desdobramento da estratégia para as áreas de manufatura, logística, compras, financeiro e RH (após realizar um evento catchball – desdobramento vertical e horizontal do processo –, a área de TI foi também incorporada ao projeto).
Além desse alinhamento das estratégias entre as áreas, todas elas incorporaram em suas contramedidas e planos de ação dos respectivos A3 filhos a aplicação de ferramentas lean (MFV, A3, TP, 5S etc.) como forma de consolidar os conceitos que até então eram aplicados apenas na manufatura.
Evitando um curso fatal para o lean
Em pouco tempo, novos projetos começaram a ser demandados (por exemplo, um projeto de logística voltado a otimizar o processo de movimentação e armazenagem de materiais). Foi nesse momento que a equipe que liderava a transformação percebeu que uma atenção especial deveria ser dada à média gestão, para que toda a transformação lean não se perdesse e tudo fosse por água abaixo.
Através de observações em muitas experiências de implementação do lean nas empresas, muitas vezes, o lean acaba morrendo na média gestão. Isso acontece historicamente tanto em pequenas empresas (no nível de supervisão, por exemplo) como em grandes empresas (na gerência, por exemplo). O objetivo era não permitir que isso acontecesse na Wabtec.
Pensando nisso, a equipe de transformação lean criou um programa chamado “Maquinista Lean” (com carga de aproximadamente 40 horas), que visava trazer aos níveis operacionais de todas as áreas envolvidas o conhecimento da cultura e das ferramentas lean. Para concluir a formação, cada participante tinha que cumprir alguns trabalhos ao longo do curso e desenvolver e apresentar um A3 com o apoio e mentoria de sua liderança imediata, aplicando ao máximo os conceitos e ferramentas aprendidas.
Como resultado dessa busca dos colaboradores da operação às suas respectivas gerências, essas lideranças que ainda não tinham ido atrás do conhecimento ou que achavam que já sabiam tudo de lean começaram a se sentir “incomodadas” e perceberam que a mudança organizacional vinha de fato acontecendo e que eles também precisavam se mobilizar para conseguir acompanhar e apoiar seus liderados e toda a transformação.
Essa ação impediu que o curso tomado por muitas organizações de “morrer na média gestão” acontecesse. Além da capacitação da operação nas ferramentas e conceitos lean, o “Maquinista Lean” veio com o objetivo de capacitar e criar uma “mobilização” na média gerência em prol das melhorias e da mudança de mindset.
Primeira versão da matriz de desdobramento pós-catchball
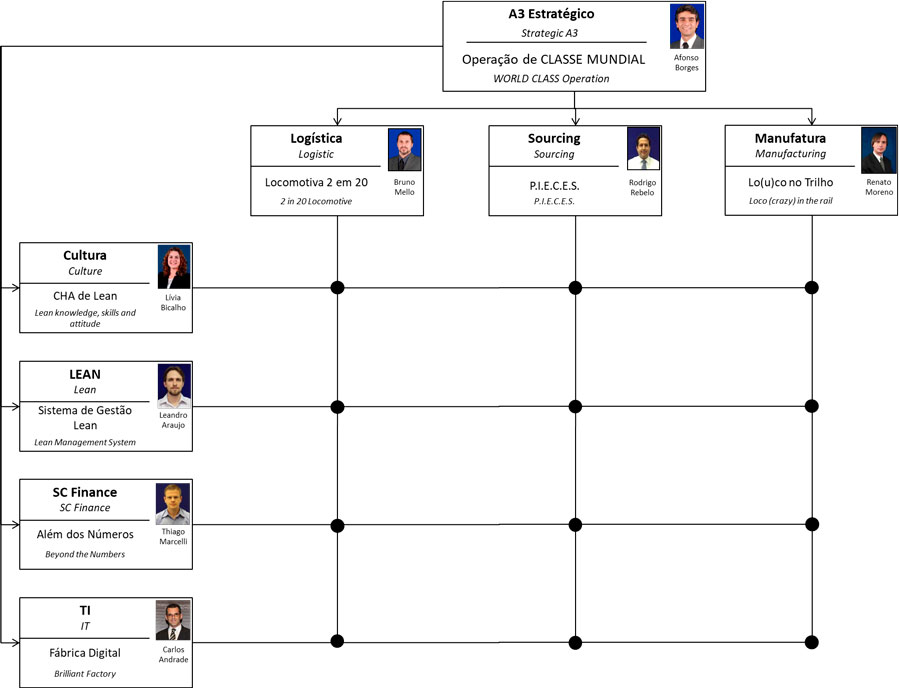
Resultados sustentáveis pedem pelo envolvimento de todos
O hoshin conseguiu um feito na Wabtec, que muitas empresas sofrem para alcançar: conectar as diferentes áreas da organização em torno de objetivos comuns e trabalhando em conjunto, como uma só equipe. Essa conexão rendeu alguns resultados visivelmente melhores em importantes indicadores para o sucesso do negócio:
- Redução de WIP em 43%;
- Redução de área necessária para a montagem de locomotivas em 1256m² – gerando a oportunidade de realizar insourcing da fabricação de cabines;
- Redução de Cycle Time e Lead Time da manufatura;
- Aumento de giro de inventário;
- Redução de acidentes de trabalho.
Este exemplo também pode ser seu!
Mesmo com resultados iniciais promissores em uma jornada lean, muitas vezes a batalha mais difícil é fazer com que os esforços não fiquem limitados a projetos isolados, mas que se enraízem na organização inteira como parte da cultura. O que a Wabtec nos mostra é como uma ferramenta lean pode ser crucial nessa difícil investida: o hoshin kanri.
Hoshin Kanri é sobre envolver pessoas, conectar os times, desdobrar a estratégia e estruturar o crescimento a longo prazo, com um caminho claro a ser percorrido por todas as áreas da empresa.
As conquistas proporcionadas pelo hoshin vão muito além do que a aplicação de qualquer ferramenta de forma isolada poderia oferecer, pois muda a cultura de uma maneira duradoura e faz com que todos os envolvidos comecem a enxergar os aspectos da transformação com outros olhos: com olhos mais lean. Esta pode ser a sua jornada também. Abra os olhos para o hoshin. Abra os olhos para o lean.
Foto tirada antes da pandemia da Covid-19
“O Hoshin Kanri foi a ‘Virada do Jogo’ da nossa operação. Com foco nos objetivos certos e uma vontade genuína de melhoria contínua, com o hoshin fomos capazes de definir a direção estratégica de longo prazo e criar um padrão de gestão que nos garantiu termos uma performance hoje melhor do que a de ontem, para sempre!”
Afonso Borges - Diretor de Operações