Esse artigo apresenta os principais conceitos, práticas e ferramentas da logística lean. Procura-se oferecer exemplos concretos, em particular, baseados nas práticas da Toyota, citadas no artigo como “cases”.
1- Introdução
A logística é a arte e a ciência de controlar o fluxo dos bens, da energia, da informação e de outros recursos como produtos, serviços e povos, da produção ao mercado. Não é possível imaginar vendas e produção sem o apoio da logística, pois essa cadeia envolve a integração da produção, do transporte, da armazenagem, do manuseio e do empacotamento.
A logística é um conceito evoluído da necessidade das forças armadas terem suprimento necessário, devido à movimentação da tropa de sua base à fronte. O dicionário Oxford define a logística como: “A filial da ciência militar, que tem como obrigação obter, manter, transportar material, pessoal e as facilidades”. Na logística militar, os peritos controlam como e quando mover recursos conforme a necessidade. Na ciência militar, diz-se que é estratégia fundamental manter um canal direto de suprimento longe do alcance inimigo, pois uma força armada (mesmo que poderosa) fica indefensável sem o suprimento de alimento, combustível e munição. A derrota dos ingleses, na guerra da independência americana, e a derrota da poderosa tropa alemã de Rommel, na segunda guerra mundial, foram atribuídas à falha logística.
Logística, como um conceito de negócio, evoluiu somente nos anos 50, principalmente devido à complexidade e à dificuldade crescentes de fornecer um serviço logístico em um contexto inicial da globalização. No negócio, a logística pode ter o foco interno (na entrada, chamada de Logística Inbound) ou externo (na saída, chamada de Logística Outbound) que cobre o fluxo e a armazenagem dos materiais do nascedouro ao ponto de consumo. Enfim, a finalidade da logística na manufatura é a de assegurar que cada máquina e estação de trabalho sejam alimentadas com o material necessário, na quantidade necessária, na qualidade necessária, no local necessário. No entanto, o “necessário” é muito subjetivo. Depende de cada ponto de vista. Na interpretação de alguns, a quantidade necessária pode ser a quantidade do mês, enquanto, para outros, pode ser o equivalente à 1h ou até mesmo conforme o takt1 segundo a tradição lean. O mesmo podemos dizer quanto ao material, à qualidade e ao local.
Então, vejamos:
Necessário
|
Sistema empurrado
|
Sistema puxado
|
Material
|
Armazenagem randômica
|
Armazenagem fixa
|
Quantidade
|
Lote 30D
|
Lote de 1h
|
Qualidade
|
Inspeção de recebimento
|
Assegurada
|
Local
|
Distante
|
Próximo ao Ponto de Uso
|
Gostaria de citar aqui um fato que esse autor vivenciou no Japão durante o seu treinamento (1991~92) no Honsha plant2 da TMC (Toyota Motor Corporation), situada em Toyota city, na grande Nagoya. Em um jornal de Nagoya, observei um artigo que fazia severas críticas à Toyota, mais precisamente ao Sistema Toyota de Produção (Toyota Production System - TPS3): “A Toyota e seu sistema apregoa uma operação sem armazéns, no entanto ela mantém seus estoques em caminhões, causando grandes congestionamentos na cercania de Nagoya.”
Sem entrar no mérito do problema controle de tráfego, que Nagoya como qualquer grande metrópole do mundo também o tem, a questão é que o jornalista não se aprofundou o suficiente em sua pesquisa para escrever tal artigo, isto é, não foi ao genba4 dos grandes armazéns verificar a confusão que estes causam ao trânsito. E mais, não citou também que os tais estoques sobre os caminhões não são estáticos, estão em movimento, eles tem um horário de partida e um horário de chegada, tendo como sistemática uma movimentação de material em pequenos lotes e alta frequência, empregando caminhões compactos (jamais grandes carretas), evitando assim a necessidade de armazenagem e toda estrutura que o acompanha, isso sem falarmos no capital de giro.
Portanto, como citei no artigo, “Como eliminar um warehouse”, este artigo vem a comprovar que o segredo não está em controlar o estoque do armazém, e sim em como fazer o Nagareka, isto é, como fazer uma logística eficiente em que o material flua como a corrente caudalosa de um rio.
2- Logística no sistema de produção em massa e enxuta
No processo convencional de transporte, alinhado à produção em massa, a economia de escala gerada com o transporte em grandes lotes é o combustível que fomenta o falso ganho e consequentemente a produção empurrada, motivo de satisfação dos operadores logísticos e proprietários de armazéns. A visão ou a pouca visão na busca de uma eficiência isolada, medida pelo custo do frete, estará criando a ilusão de um falso ganho por quilômetro transportado. Senão, vejamos, é verdade ou mentira a queixa dos responsáveis pelo recebimento e expedição quanto ao mau aproveitamento pleno da capacidade de recebimento e expedição? A verdade é que as suas noventa e nove docas de expedição às 17h00 estão totalmente tomadas de carretas para Outbound e Inbound, porém às 7h00 as docas estão desertas ou quase desertas, pois as “sempre bem-vindas pombas urbanas” estão ao deleite de seu desjejum matinal, deliciando-se dos grãos de milho derramados no dia anterior pelos caminhões dos fornecedores de matéria prima.
O contraste disso é a cercania externa à expedição, onde observo um mar de caminhões ocupando todas as ruas do bairro (!). E o pior. Observa-se um “buzinaço” ensurdecedor da vizinhança querendo sair de suas respectivas garagens para levar as crianças à escola no dia da prova global. A placa de “proibido estacionar” está sendo obedecida sim, mas somente pelo cavalo mecânico, pois a carreta e os bitrens ocupam quase que completamente a quadra.
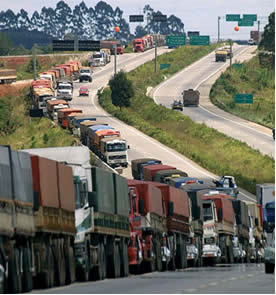
Moral da história: durante o mês, o Planejamento e Controle da Produção, que tem uma sabia bola de cristal, ordenou suprir, produzir e estocar exatamente os produtos que o meu cliente não os deseja mais na quarta semana do mês, e neste momento está tendo de produzir de última hora o produto que não constava nem em previsão, mas que as vendas efetuou uma grande negociação para entrega imediata. A logística, por sua vez, apesar das insistentes cobranças de entrega, quer otimizar o frete e reter o caminhão na doca que é compartilhada com o Inbound, a fim de completar a carreta com os produtos que ainda estão na máquina. Por sua vez, os caminhões com as matérias primas, providenciadas às pressas, aguardam poder adentrar a uma das noventa e nove docas com a sua grande carreta estacionada em frente à garagem da dona “Lucinha”, que quer sair a tempo de seu filho ainda poder fazer a terceira prova do dia.
Esta é uma história verídica ou inverídica? Não ocorrem todos os dias, ocorre somente no condomínio industrial vizinho de diferente segmento, jamais em nossa empresa.
Se transportarmos isso para o mundo futebolístico, seriam as tais jogadas individuais com dribles no meio de campo sem um objetivo claro de conduzir a bola em direção ao gol. Realmente, na esmagadora maioria das empresas, cada setor foca somente no seu desempenho individual, independente de qual é a necessidade do negócio. O comprador, por exemplo, buscará a melhor oportunidade de compra em preço e volume. A produção irá buscar a capacidade máquina máxima para um volume não necessariamente vendável. As vendas farão grandes vendas concentradas sem se importar com o mix de forecast passado por ele mesmo (a maioria nem isso passam, em geral são valores em reais ou em toneladas). E finalmente, o Transporte irá ocupar as docas durante longas horas com os maiores equipamentos, com o menor frete, solicitando a carga e a descarga de todo o material vendido e comprado por oportunidade.
A questão é:
- Será que o comprador verificou o estoque genchi genbutsu5e negociou o espaço disponível no almoxarifado, ou será que verificou em seu computador somente o saldo informado pela famigerada MRP6?
- Será que a produção buscou produzir somente o que foi vendido, ou produziu capacidade máxima, tudo e mais um pouco do programa mensal, e empurrou tudo à expedição? Será que se preocupou em verificar se o que produziu é o requerido para o embarque?
- Será que as vendas se preocupou em estabelecer uma meta por SKU7? Ou será que a meta foi estabelecida em toneladas e em reais de faturamento? Será que as ações agressivas de vendas foram realizadas para cumprir a meta do dia ou esta foi efetuada nos últimos dias do mês?
- E finalmente, será que o transporte buscou o equipamento adequado para coletar continuamente pequenos lotes de carga, ou passou a metade do dia procurando pelo menor frete?
Seja o que for, concordam que teremos materiais parados no recebimento, no almoxarifado, em processo, na expedição e nos caminhões incompletos na doca?
Quais decisões seriam tomadas após dias repetindo o cenário acima?
> Aluguel de tendas para o Inbound?
> Terceirizar determinados processos e encomendar máquinas importadas?
> Alugar armazéns externos para o Outbound?
> Alugar pátios para caminhões e exigir das transportadoras chegadas com antecedência
de 1 dia, tanto para Inbound, como para Outbound?
Conseqüência: Sangria desatada no fluxo de caixa.
No modelo competitivo de transporte, é a alta frequência em pequenos lotes que sustenta e fundamenta o sistema puxado. Foi, como sempre, a Toyota o pioneiro na implementação da logística Round Trip8 e Milk Run9 na América do Sul, cuja coordenação dos projetos foi de responsabilidade desse missivista, liderando um time multidisciplinar de engenheiros ligados a departamentos de compras, comércio exterior, PCP e logística. A época no início dos anos 90, até já se notava timidamente (estampando Milk Run na lona de seus siders10) operadores logísticos trabalhando com janelas de entrega e com uma frequência um pouco maior de entrega em relação ao convencional, mas nada que se compara a uma verdadeira logística controlada de transporte em alta frequência e em pequenos lotes.
O pai do TPS, Taichi Ohno, deixou um legado de sete fundamentos muito claros de se praticar na companhia, ou melhor, combater e eliminar:
- Desperdício de produção em excesso;
- Desperdício de estoque;
- Desperdício de processamento desnecessário;
- Desperdício de retrabalho;
- Desperdício de adiantar;
- Desperdício de transporte.
Ao ingressar na companhia (Toyota do Brasil - TDB11), fui alocado à Divisão de Controle de Produção, mais precisamente como engenheiro responsável pelo PCP; melhorias na logística, controle de materiais e coordenação de Ordem de Modificação de engenharia (OM12).
Uma das primeiras missões atribuídas a mim foi a de melhorar toda a movimentação de material dentro da fábrica e, pasmem, o mais espantoso para este leigo na época foi ter recebido como ressalva que transporte é um desperdício, isso para um engenheiro recém-ingressado na companhia quase sem nenhuma noção de TPS, a não ser ter lido algo como um tal de kanban13 empregado na produção de algumas companhias japonesas, soava como um paradoxo. Imaginem vocês o nó na cabeça do jovem engenheiro! Como efetuar melhorias na movimentação de materiais ouvindo logo de início uma ressalva dessas? Mais tarde vim a entender que, por isso mesmo a logística deveria ser executada de uma forma eficiente, de forma que conectasse todos os processos com um fluxo ininterrupto.
Mas falemos de alguns projetos logísticos que serviram como balão de ensaio para no futuro virmos a implementar o projeto de TPS Inbound e Outbound no Brasil.
3- O que é Logística Lean no Inbound
É o próprio JIT e tem como objetivo manter o fluxo de material abastecido com a entrega do material necessário, quando necessário, na quantia exata necessária, e acondicionado pronto para uso.
- A logística Lean mantém o abastecimento através da manutenção do fluxo, e não através da geração de estoques.
- Criação de valor na logística Inbound – cliente: produção.
- O valor do tempo certo - fornecer o suprimento no momento em que o item estiver em produção.
- O valor do local certo – fornecer o insumo o mais próximo ou no exato ponto de consumo.
- O valor do acondicionamento certo – minimizar a movimentação e manter a segurança.
Interessou-se pelo tema? Veja o nosso treinamento de Logística Lean Inbound
4- Case Inbound
Em 1994 foi implementado o projeto CKD14 de produção do motor 14B que veio a substituir o robusto motor OM-364 comprado da Mercedes Benz do Brasil, que até então equipava a também robusta família de utilitários Bandeirante OJ-55 (derivado do Land Cruizer FJ-45). Esse projeto que a matriz considerava como um balão de ensaio para os grandes projetos futuros na América do Sul tem como base técnica o time de engenharia simultânea (36 engenheiros, todos treinados na TMC no início dos anos 90) da TDB. Como integrante desse seleto grupo, fui o responsável pela coordenação do projeto e pelos trabalhos de PCP e logística. Falando especificamente da logística que nos interessa nesse momento, no transporte marítimo foi implementada a logística com um lead time15 de 35 dias no mar, a frequência semanal de chegada de 2 contêineres de 20ft (equivalente a aproximadamente 6,10 m) para produção de 75 veículos/semana naturalmente qualquer entendedor da indústria automobilística diria que isso é em volume irrisório, poderia ser tratado, na melhor das hipóteses, com uma frequência mensal de navios e não semanal. No entanto, aí está o diferencial da logística convencional da produção em massa e do TPS, pois a prática desse sistema não permite condescendência a um dos maiores desperdícios, que é o estoque. Para se ter uma noção da ordem de grandeza, um dos maiores fabricantes de caminhões no Brasil monta esse mesmo volume diariamente, e nas linhas de montagem de carros populares, 10 vezes esse volume em um turno da produção. Na TDB, mantinham-se 10 dias de estoque dos componentes desse motor, 5 dias de giro e 5 dias de segurança (greve da aduana e acidentes), então todo e qualquer revés deveria ser suportado por esse estoque. Isso foi comprovado na prática. Posso citar o caso de um naufrágio do navio que transportava os contêineres da Toyota já aqui no Brasil, na entrada do porto de São Francisco, em Santa Catarina, e a perda desses contêineres foi perfeitamente suportada pelo estoque de segurança. Essa prática nos levou a comprovação de que, mesmo tendo uma grande distância (outro lado do mundo), é possível se praticar uma frequencia constante de entregas em pequenos lotes possibilitando trabalhar com baixo nível de estoque e otimizando o fluxo de caixa da companhia.
A experiência adquirida em movimentar materiais em pequenos lotes com alta frequencia foi fundamental na idealização de projetos logísticos de novos produtos e de novas plantas da Toyota na América do Sul, principalmente na Argentina e no Brasil com o advento do MERCOSUL, lembram-se dele, de protecionismo em protecionismo, por incrível que pareça ela ainda está ai, sobrevivendo.
Em 1995 foi definida a introdução de um novo produto na América do Sul, um mercado ainda pouco explorado pela Toyota, mas considerado estratégico por ser um dos dois grandes mercados de grande potencial no mundo a ser desenvolvido (o outro era a China que mais tarde veio a confirmar esse potencial com um crescimento estratosférico).
Após um minucioso levantamento técnico de fornecedores e de custos nos dois principais países integrantes do MERCOSUL, Brasil e Argentina, foi definida a Argentina, mais precisamente Zarate, um pequeno município da província de Buenos Aires, como sendo o local que abrigaria a nova planta (TASA - Toyota Argentina S/A) de uma família de veículos utilitários Hilux, que viria a substituir mais tarde os robustos Land Cruiser Bandeirante, produzido na planta de São Bernardo do Campo. Não vamos discutir o mérito da escolha, mas o Brasil, por possuir um parque industrial de autopeças muito mais avançado, e a própria TDB, pela sua capacidade produtiva e principalmente pelo seu corpo técnico altamente capacitado, todos treinados na TMC, foram designados a fornecer as principais peças componentes do veículo. Era um grande desafio a implementação de uma logística que consistia em importar sub-componentes, nacionalizar componentes, montar conjuntos e enviar à TASA em formato de CKD. A esse projeto foi designada a nomenclatura de PJT-AR/BR e, como case de logística, estarei explanando a sistemática adotada para o projeto que foi implementado com o suporte da LAD16 e da OPPD17 da Toyota Motor Corporation (matriz). Segue a sequência de desenvolvimento:
a) Capacidade do equipamento (é a base para definição do lote):
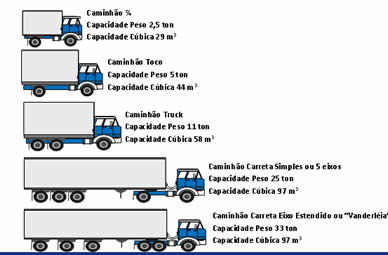
b) Definição do lote (Kit):
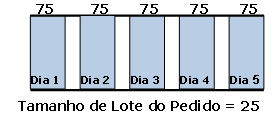
c) Desenvolvimento de embalagens retornáveis:
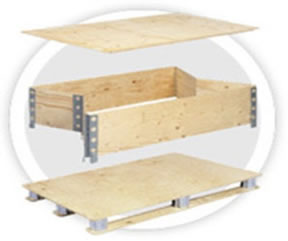
d) Modulação de carga:
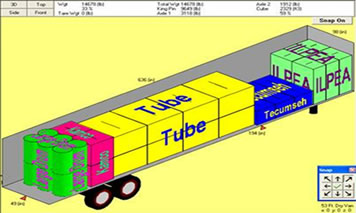
e) Percurso de rota:
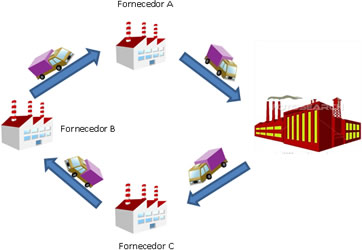
f) Quantidade de equipamento na rota:

5- Case Consolidação da carga:
As peças a serem enviadas à TASA consistiam basicamente em componentes produzidos pela TDB, tais como peças estampadas de carroceria (portas, capo, para lama, teto), longarina do chassi, travessas do chassi, gancho fundido e usinado, conjunto eixo traseiro (4x2; 4x4) montado. A outra parte consistia em peças externas compradas, tais como faróis, lanternas, caliper, disco do freio, grade do radiador pintado, grade do radiador cromado, entre outros, que eram entregues na planta de São Bernardo em lotes diários. Essas peças eram consolidadas, embaladas no formato de kit de 15 (veículos) em caixas retornáveis, e finalmente despachadas em uma janela de expedição em intervalos de 2 h.
Considerando o mix de produção na TASA, o mesmo mix foi empregado no transporte dos kits. E considerando a melhor eficiência no aproveitamento carga (90%), foram estabelecidos três mix (A, B e C) de modulação de carga.
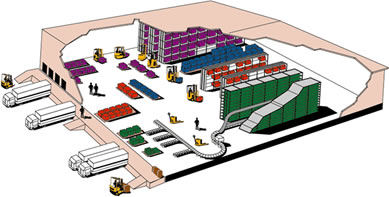
6- Case Desenvolvimento de Embalagem:
Foi um trabalho meticuloso de engenharia logística no qual foram utilizadas caixas do tipo “clip lock” (painéis presos por clip de aço mola) facilmente desmontáveis, e desenvolvidas mioleiras internas (madeira e EVA) de fixação das peças que garantissem a qualidade em um percurso rodoviário de 2500 km com piso extremamente ruim. Para garantir a qualidade, sucessivos testes de resistência e corrosão foram realizados:
- Teste de resistência: Empilhadeiras com a caixa contendo peças correndo sobre obstáculos de ripas de madeiras, caixas sendo largadas de uma altura de 0,5m, enfim foi simulado o péssimo piso da estrada na qual as peças seriam submetidas.
- Teste de corrosão: Como havia a premissa de que não haveria um processo de desengraxamento na TASA, não poderíamos empregar óleos de proteção, foram então desenvolvidos e realizados exaustivos testes contra corrosão, empregando papéis e plásticos VCIs, onde as peças “embrulhadas” e acondicionadas dentro das caixas ficaram expostas ao tempo durante 30 dias (condições em que jamais as peças seriam submetidas nem em trânsito, nem na TASA).
Enfim, relatamos aqui como o alto padrão de qualidade exigido pelo TPS foi garantido pela engenharia logística da TDB no transporte das peças brasileiras.
7- Case Entrega Direta:
Neste projeto (321N, mais conhecido internamente como PJT-AR/BR), apesar de o negócio ter designado a logística como FOB, isto é, a TASA sendo responsável pelo frete e coletando as peças na TDB, mas, por serem empresas do grupo, na prática adotamos uma logística de controle misto, isto é, com o controle e a responsabilidade de entrega a cargo da TDB. A essa logística se deu o nome de “Round Trip”, com os caminhões transportando peça para Argentina e voltando com as caixas retornáveis, portanto nem sempre com bom aproveitando de carga na volta, mas sempre com carga. Como os caminhões partiam em um intervalo de 2h, no total de 4 caminhões por dia (1 turno), isso significa que havia um comboio separado em um intervalo de 2h entre eles. Hoje com a demanda em alta, essa logística está sendo realizada com 16 caminhões em um intervalo de 1h entre eles.
Podemos definir essa logística de entrega direta como uma grande quebra de paradigma, pois, apesar da distância de 2500 km separando duas plantas de diferentes países e que não necessariamente tem de ser de carga fechada ou um volume grande do mesmo produto, ela pode ser realizada em kits de pequenos lotes e grande frequência de entrega.
Na parte burocrática, para viabilizar e cumprir regiamente o lead time de 3 dias, o documento de exportação é providenciado com antecedência de 24hs (trâmite de exportação) e enviado à fronteira (Uruguaia) via courrier, a fim de garantir um desembaraço rápido de exportação, isto é, com essa providência, o trâmite de desembaraço estará pronto quando o caminhão chegar a fronteira depois de 2 dias em trânsito no território brasileiro.
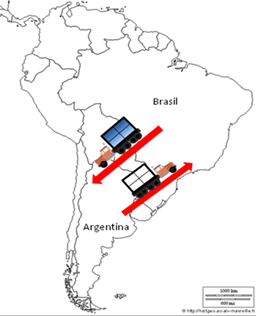
8- Controle
Seja qual for a modalidade de logística adotada (entrega direta; coleta; consolidação; cross docking18), o controle é a parte fundamental de toda e qualquer operação logística, na verdade muitos “entendidos” vendem projetos logísticos, salvo raras exceções, a esmagadora maioria falha neste quesito. Vejo muitas estampas com a “frase” Milk Run em seus vistosos caminhões siders; já presenciei ilustres palestrantes de operadores logísticos apresentando projetos de Milk Run; e transportadores participando de BID19 garantindo entregas on time20 (naturalmente embutindo gordura no L/T). No entanto, nenhum deles apresentam um controle visual coerente às pessoas que irão operar o sistema. Senão, vejamos, quando visitamos uma doca de expedição ou recebimento, raramente conseguimos visualizar se a operação está on time, atrasada ou adiantada. É muito fácil também apresentar um projeto dizendo que tem de haver controle nas janelas, mas como se faz isso na prática? Na realidade a pergunta é como vou controlar a janela sem controlar a cadeia toda. É obvio que se não controlar a saída do caminhão na origem (no caso Inbound) e também no trajeto, não posso garantir a chegada. Muitas vezes ouço nas reuniões matinais de empresas, o responsável do suprimento explanando sobre materiais crítico que estão previstos para serem recebidos no dia, e quando pergunto, quando e a que horas o caminhão partiu da origem, a resposta invariavelmente é, não sei, coloquei a data de minha necessidade e a obrigação é do fornecedor cumprir o prazo, a mim só resta ficar na porteira esperando “o ente querido chegar”. Isso ainda é o lado bom da estória, o que acontece na maioria dos casos é o leite derramado, isto é, prazos vencidos, estoque zerado e a operação parada por falta de material.
Os controles mínimos necessários são:
- Quadro de controle do caminhão em trânsito e da janela de chegada: Plan x Real;
- Quadro de controle de recebimento de material (fornecedor, tipo, quantidade): Plan x Real;
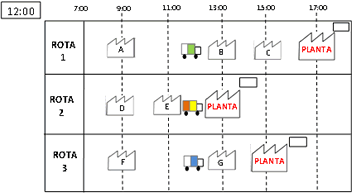
- Fluxograma de cadeia de ajuda e contato em cada fornecedor e transportador;
- Fluxograma de cadeia de ajuda interna;
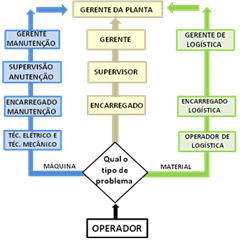
Enfim, tudo deve estar planejado, visível e à prova de surpresas.
9- Case planejamento
Ao receber o pedido mensal com a premissa de mês N fixo e os forecast N+1 e N+2 pode-se haver tolerância de mais ou menos 10% e 20% respectivamente.
Despatch Plan: Com base nesse pedido que se recebe em D20 de N-1, confecciona-se o plano de despacho mensal (explodido em diário) que, por sua vez, é desdobrado em vanning plan21 obedecendo o mix de modulação e este, por sua vez, é desdobrado ao plano de produção e ao pedido aos fornecedores.
10- Janela de Recebimento
A janela de recebimento, ao contrário do que a primeira vista pode parecer, não é somente uma ordenação de chegada para entrada de caminhões, ela faz parte integrante importante do nagareka sistêmico e do estoque (baixo).
A janela como em toda cadeia logística, deve ser montada com um Pitch22 semelhante ao takt e ao mix de produção do processo cliente para que se mantenha o fluxo sem interrupção, mantendo o material em movimento.
No momento em que o material ficar estacionário, é o momento em que esta se converte em estoque. Ao montar a janela, as regras devem ser estabelecidas de uma forma clara e rígida conforme se segue:
- A sequência da grade da janela de recebimento deve obedecer a sequência e o ritmo de consumo que é o do processo cliente;
- A grade de janela ideal é aquela que obedece a um programa fixo nivelado de volume de carga e que mantém, assim, uma quantidade fixa de recebimento de caminhões distribuídos equitativamente dentro da jornada de trabalho igual ao do processo cliente, isto é, seguindo o mesmo ritmo e turno de trabalho;
- Em uma empresa que ainda não atingiu um estágio nivelado de trabalho em sua cadeia de negócios, isto é, existe dentro do mês uma variação tanto no volume como no mix, é um pouco mais complicado a implementação de uma grade de janela fixa, mas ainda assim é possível implementar uma janela flexível, mas que se enquadre na grade pré-estabelecida.
Seria uma janela que lembra um pouco a grade de um aeroporto, isto é, pode haver uma certa variação no mix de caminhões a receber, mas enquadrado a grade com os horários pré-estabelecidos. Naturalmente é uma operação que deverá carregar uma dose razoável de MURI23 devidos ao MURA24 e resultando, assim em alguns MUDAs25 indesejáveis, mas é o preço que se pagará pela falta de HEIJUNKA26. Costumo chamar esse tipo de grade de janelas flexíveis, seria um estágio intermediário administrável para no futuro buscar uma grade de janela fixa (temos cases práticos de implementação em empresas dentre os projetos desenvolvidos pelo Lean Institute Brasil).
No case projeto 321N do Hilux, tanto a janela de coleta nos fornecedores, como na janela de recebimento e despacho, sempre de manteve a janela fixa. Como sempre no TPS tudo é no binário, ou é ou não é.
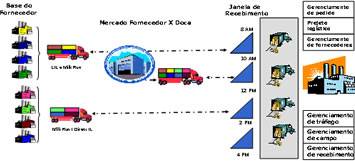
11- Cross docking
Essa é uma modalidade de logística semelhante a um entreposto, ou seja, é uma versão aperfeiçoada de consolidação simples de carga. Mas diferentemente da consolidação de carga, nesta modalidade não deve haver armazenagem, os caminhões chegam a uma plataforma compostas de docas de recebimento e despacho. Em seguida transferem-se rapidamente as cargas diretamente de um caminhão para outro, assim, apesar do handling a mais, evita-se o estoque intermediário e consegue-se uma otimização na operação logística com um bom aproveitamento de eficiência na carga. É muito empregada em longas distâncias com origens e destinos distintos, isto é, consolida-se rapidamente na própria plataforma materiais com destino comum. Portanto, o principal mérito dessa modalidade é a velocidade e o transporte em lotes pequenos e/ou lotes fracionados.
De novo o controle de chegada, saída do caminhão, e em trânsito é fundamental para que possamos sincronizar a operação. Para implementar, recomenda-se o emprego do Trabalho Padronizado implementado após uma análise minuciosa do TCTP (Tabela Combinada de Trabalho Padronizado). Sim, é isso mesmo, é mais uma quebra de paradigma. O TCTP não é aplicado somente onde se envolvem o trabalho homem e máquina automática, poderá sim ajudar em uma análise com a finalidade de sincronizar a operação logística.
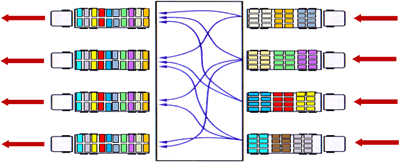
12- Case Milk Run
Em 1996, o sonhado projeto de uma nova planta para produção de um novo produto, o Corolla, produto mais popular da Toyota e de maior número de vendas no mundo, foi definido como uma continuidade da estratégia de avanço no mercado sul- americano, a construção de uma nova planta no Brasil, mais precisamente no município de Indaiatuba (região de Campinas). Então, antes mesmo do lançamento desse projeto (PJT-044N), a poderosa LAD da matriz iniciou, em conjunto com a engenharia logística da TDB, coube novamente a este missivista, os estudos preliminares de logística para viabilização do projeto, pois já se sabia de pesquisas anteriores que o custo Brasil logístico (custo proto; custo rodoviário) era um dos mais altos do mundo. Mesmo sem essas premissas, é praxe na Toyota o grupo de logística juntamente com a engenharia de produto, serem sempre os primeiros a dar início aos trabalhos, pois dois dos maiores desperdícios citados por Ohno san, que são o transporte e o estoque, devem ser minuciosamente estudados e segurados no menor nível possível. Devido ao baixo índice de nacionalização na área de logística da planta, foi privilegiada a área de armazenagem para os kits CKDs importados e praticamente zero de área para os componentes nacionais, isto porque desde o início foi idealizado o recebimento de pequenos lotes destas peças. A logística idealizada foi então um mix de logística constituída da seguinte forma:
1- Modalidade logística por região:
a) Fornecedores de longa distância (acima de 300 km): Entrega direta (FOB27)
- Curitiba (PR): 1 Fornecedor
b) Fornecedores até 200 km: Milk Run
- Rota Sul de Minas: 3 Fornecedores
- Rota região de Campinas: 5 Fornecedores
- Rota região de S.Paulo: 7 Fornecedores
- Rota interior de S.Paulo (Tatuí e Jundiaí): 2 fornecedores
c) Regras
- Horas paradas nas janelas do fornecedor: 15 min + tol. de 5min.
- Anomalias: Informar e solicitar orientação à central de controle na TDB.
Ex.: Possibilidade de exceder o tempo de tolerância.
2- Bid: Com a modalidade definida, listam-se as premissas do Bid:
- Montagem da melhor rota: O transportador tem a liberdade de montar a proposta com alternativas e/ou até desmembrando a rota;
- Controle: O transportador deverá apresentar a sua capacidade de controle dos caminhões em trânsito;
- A cotação deve ser com custo aberto detalhado em reais por quilômetros rodados; horas parada (pedágios, seguros etc.);
- Os transportadores pré-selecionados (três no máximo) receberão a cartilha com o escopo do projeto, terão 10 dias para estudar e elaborar a proposta;
- As apresentações (10min) deverão ser agendadas, todas no mesmo dia e em horários distintos pré-estabelecido. Naturalmente para concorrentes de um Milk Run, a pontualidade da apresentação deverá ser considerada.
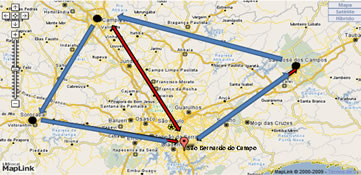
3- Modulação de carga
a) Definir os equipamentos a serem utilizados em cada rota;
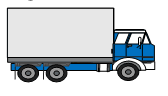
b) Utilizar o máximo possível das embalagens pré-existentes no fornecedor;
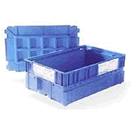
c) Desenhar a modulação de carga com as embalagens dos fornecedores e, caso necessário, desenvolver adaptadores que permitam empilhamento entre embalagens distintas;
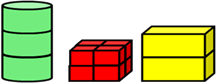
d) Definir um escopo de projeto a médio prazo de miniaturização e padronização de embalagens empilháveis.
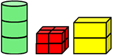
13- Conclusão
Apresentamos os principais elementos da Logística Lean com exemplos práticos da Toyota. Não existe somente uma única forma de implementar um projeto de logística, seja ela Inbound ou Outbound, deve-se estudar conjuntos de formatos logísticos que interajam entre eles, tornando o sincronismo da operação o mais harmonioso possível como o fluxo caudaloso de um rio, isto é sem represamentos (material parado gerando estoque), focado na constância e no menor Lead Time.
Apêndice
- Takt = Tempo disponível para a produção dividido pela demanda do cliente.
- Honsha Plant = Antiga Koromo plant, uma das fábricas da Toyota Motor Corporation (TMC).
- TPS = Toyota Production System. Sistema de Produção da Toyota.
- Genba = Termo japonês para “local real”, normalmente utilizado para o chão de fábrica ou qualquer lugar em que ocorre o trabalho que cria valor.
- Genchi genbutsu = Prática vigente na Toyota que consiste em compreender plenamente determinada condição através de observação pessoal direta da realidade.
- MRP = Material Requirement Planning = Planejamento das Necessidades de Materiais.
- SKU= Stock Keeping Unit ou Unidade de Manutenção do Estoque. Designa os diferentes itens de um estoque, normalmente associado a um código identificador.
- Round Trip = Viagem completa, ou seja, os caminhões que transportavam cargas eram utilizados na ida e na volta.
- Milk Run = Método de acelerar o fluxo de materiais entre plantas no qual os veículos seguem uma rota para fazer múltiplas cargas e entregas em muitas plantas.
- Siders = Caçamba de caminhão coberta com fechamento lateral de Cortina Corrediça.
- TDB = Toyota do Brasil.
- OM = Ordem de Modificação de engenharia = Alteração na especificação e ou desenho de produto.
- KANBAN = Dispositivo sinalizador que autoriza e dá instruções para a produção ou retirada de itens em um sistema puxado.
- CKD = Complete Knock Down = Conjunto (de peças) totalmente desmontados.
- Lead time = Frequência com que uma peça ou produto é completado por um processo, conforme cronometrado por observação.
- LAD = Logistic Administration Division.
- OPPD = Overseas Production Planning Division.
- Cross docking = Instalação que seleciona e (re) combina uma variedade de intens advindos de diversos fornecedores para que sejam enviados aos vários clientes.
- Bid = Concorrência para contratação do melhor serviço.
- On time = Significa que um processo está sendo feito no momento certo, ou seja, não está atrasado e nem adiantado, está na hora certa.
- Vanning plan = Plano de carregamento.
- Pitch = Quantidade de tempo necessária em uma área de produção para completar um contêiner de produtos.
- MURI= Sobrecarga de equipamentos ou operadores, exigindo ritmo mais intenso ou acelerado, empregando mais força ou esforço, por um período de tempo maior do que podem suportar.
- MURA = Falta de regularidade em uma operação.
- MUDA = Qualquer atividade que consuma recursos sem criar valor para o cliente.
- HEIJUNKA = Nivelamento do tipo e da quantidade de produção durante um período fixo de tempo.
- FOB = Free On Board: Retirada e frete pago pelo cliente.
Nelson Eiji Takeuchi
É gerente de projetos do Lean Institute Brasil. Engenheiro tendo atuado por 15 anos na Toyota do Brasil dentre os quais 1,5 anos em OJT na matriz Toyota Motor Corporation (Japan) focado em TPS, Controle de Produção, Logística e Suprimentos. Na Toyota do Brasil iniciou como Engenheiro Pleno e alcançou a posição de Gerente de Área da Administração Industrial, gerenciando Controle de Produção; Logística; Comercio Exterior; Suprimentos; Controle de Qualidade; Engenharia Predial; Meio Ambiente; Segurança do Trabalho; Projetos; etc. Atuou ainda na ARTEB como Gerente de Manufatura; na Sumidenso como Gerente de PCP / Suprimentos e na NEC do Brasil como engenheiro.
Agradecimentos
Ao apoio técnico de Juliana Santo, Tamiris Masetto na revisão de texto e ao incentivo de José Roberto Ferro. Graças a inestimável colaboração dos mesmos, está sendo possível a publicação desse artigo.