Tradução: Odier Tadashi.
Compilado em Outubro de 2003 pela Divisão de "Public Afairs" da Toyota Motor Corporation.
Na Feira de Soluções de Sistemas para Peças Automotivas 2003, sediada em Tóquio no dia 18 de Junho, Teruyuki Minoura, então comandando a direção global de compras da Toyota Motor Corporation, falou sobre suas experiências com o TPS (Sistema Toyota de Produção) e o que isso significa para os seus fornecedores e para o futuro da indústria automotiva.
Teruyuki Minoura tem confiança que os princípios há muito tempo estabelecidos do Sistema Toyota de Produção não mudarão no futuro e que o TPS será capaz de enfrentar qualquer desafio. Ele destaca que originalmente o sistema surgiu de uma abordagem baseada em tentativa e erro voltada para solucionar problemas práticos e atender as necessidades da companhia. Relembrando as memórias dolorosas da disputa trabalhista de 1950 que destruiu muitas amizades, ele observa que: "O negócio sofre se os esforços são voltados para aumentar a produtividade mas os produtos não vendem". Foi através de tais experiências que surgiu o conceito básico do Just-in-Time.
Da forma mais simples, Just-in-Time é "tudo o que diz respeito a produzir e transferir apenas o que é necessário", segundo Minoura. Ao invés do antigo sistema de produção "empurrado" de baixo para cima, o Just-in-Time representa a mudança para o sistema "puxado" onde os trabalhadores apenas produzirão o que é necessário. Ferramentas, como o sistema kanban (cartão de informação), andon (painel de informação) e o pokayoke (prevenção de erros) foram desenvolvidos para implementar o sistema puxado. Entretanto, Minoura alerta, "a simples introdução dos cartões kanban ou dos painéis andon não significa que você conseguiu implementar o Sistema Toyota de Produção na sua indústria, já que são nada mais do que meras ferramentas. As novas tecnologias de informação também não fogem a regra, e também devem ser aplicadas e implementadas como ferramentas".
No começo de sua carreira, Minoura trabalhou sob a supervisão de Taiichi Ohno, reconhecido como o criador do Sistema Toyota de Produção. Ohno, através de uma incansável abordagem de tentativa e erro, trabalhou para colocar em prática um sistema de produção "puxado" que parasse a fábrica quando itens desnecessários fossem produzidos. Mas Minoura ressalta que foi apenas através do aperfeiçoamento de uma "conjunto de ferramentas isoladas" em um sistema completamente desenvolvido, nomeado Sistema Toyota de Produção (TPS), que eles foram capazes de disseminar esse conceito por toda a empresa.
Um Sistema "Puxado" precisa de trabalhadores que usem a cabeça
Para Minoura, o método pelo qual o TPS desenvolve os trabalhadores é a sua principal característica. "Em um sistema ‘empurrado’, há pouca oportunidade para que os trabalhadores aumentem seus conhecimentos porque eles apenas trabalham, produzem de acordo com as instruções que lhe foram dadas. Por outro lado, o sistema ‘puxado’ pede que o trabalhador use sua cabeça para lidar com um processo de fabricação onde ele deve sozinho decidir o que é necessário ser feito e com qual velocidade é preciso ser feito".
"Um ambiente onde as pessoas têm que pensar traz consigo a sabedoria, e essa sabedoria traz junto o kaizen (melhoria contínua)", destaca Minoura. "Se fosse solicitado produzir apenas uma peça por vez, para produzir de acordo com o fluxo, um típico operário de linha acabaria ficando confuso. Uma característica básica do ser humano é buscar mais conhecimento quando está sob pressão. Talvez a principal força do Sistema Toyota de Produção seja o método como desenvolve as pessoas". É por isso que quando Minoura explica o TPS, ele fala que, na verdade, o T significa "Thinking", ao invés de "Toyota".
No TPS, o T também significa "Thinking"
Relembrando quando Ohno lhe pedia para resolver problemas, Minoura fala, "Eu não acho que ele estava completamente interessado na minha resposta. Eu acho que ele estava apenas me colocando em algum tipo de treinamento para que eu aprendesse a pensar". Similarmente, a Harvard Business School usa o método do caso-estudado como melhor alternativa para treinar pensadores de negócios. Os professores de Harvard nunca passam aos estudantes a resposta, porque, mais uma vez, esse não é o objetivo. Minoura fala que "Desenvolver pessoas é o ponto inicial para o monozukuri (fazer coisas) na Toyota".
Para diminuir o Lead Time, elimine tudo que não agrega valor
A implementação da produção Just-in-Time começa com a redução do lead-time parafazer coisas, de acordo com Minoura. "O caminho para diminuir o lead time é eliminar tudo que não agregue valor. Há apenas alguns processos que realmente envolvem produção. Na maioria do tempo, o material é apenas transferido de um lugar para o outro. Se isto causa um aumento considerável no lead time, se livrar urgentemente dessas etapas onde nada está sendo processado é algo que deve ser feito o mais breve possível".
Em seguida, alguém deve se livrar dos defeitos. "Se um item é defeituoso, ‘o que é necessário’ não poderá ser entregue. Se um defeito é encontrado, a linha deve parar naquele exato momento para que as medidas visando solucionar este problema possam ser tomadas. Isso caracteriza o conceito de construir qualidade no processo". Minoura adiciona à explicação: "Produzir o que é necessário significa produzir a quantidade correta do que é necessário. A resposta é um sistema flexível que permite à linha produzir a quantidade certa do que é necessário. Se é preciso ter seis operários para produzir uma certa quantidade de um item e há uma queda na quantidade requerida, então seu sistema deveria ser capaz de liberar uma ou duas pessoas para fazerem outro serviço".
A linha deve parar se há um problema
Painel luminoso Andon.
É essencial parar a linha quando há um problema. "Se a linha não parar, os itens defeituosos inúteis irão ser levados para o próximo estágio. Se você não sabe onde o problema ocorreu, você não pode fazer nada para consertá-lo. É dai que vem o conceito do controle visual. A ferramenta para isso é o painel luminoso andon".
Cuide dos defeitos apenas quando eles ocorrerem e a quantidade de pessoas que você precisa irá diminuir
Trabalho padronizado é essencial para identificar onde as coisas estão dando errado, Minoura diz. "Se você está lidando com algo que se encontra diferente do que está na folha de trabalho padronizado, ou diferente do modo como os outros estão fazendo, então isso é a definição de um problema. Ao pensar sobre o que está causando o problema, este se tornará visível. Quando o problema se torna claro, abrem-se as portas para o kaizen. Se você tornar regra cuidar dos defeitos apenas quando eles ocorrem, então a quantidade de pessoas irá cair acentuadamente. Aquilo que está rodando sem dificuldades ou interrupção não precisa estar sob supervisão. Se você se comprometer a apenas encontrar e consertar os problemas, você será capaz de ter um controle efetivo da sua linha com um número menor de pessoas".
Pergunte a si mesmo "Por que?" cinco vezes
Quando acontece algo errado, a primeira coisa a ser feita é consertar o erro. Minoura recorda que Ohno costumava pedir a eles para se perguntarem "Por que?" cinco vezes seguidas porque "assim você encontrará a raiz do problema e se você conseguir eliminá-la, para nunca mais acontecer de novo". Entretanto, Minoura enfatiza que observar o prórpio local onde aconteceu o problema ao invés de deduzir a partir do escritório o que ocorreu é a única maneira correta de se responder aos "Por que?". "Eu sempre sou levado a pensar que o método dos Cinco Por quês não está funcionando como deveria porque há falta de treinamento prático. A razão para isso é que eles sempre acabam retornando para o método da dedução. Sim, dedução. Então quando eu pergunto a eles "Por que?", logo eles me reportam cinco causas, tão rápido quanto um flash de luz, por dedução. Então novamente eu perguntava cinco vezes "Por que?"para cada uma das causas que eles me deram. O resultado foi que eles começaram a deduzir mais uma vez, e são tantas causas dadas na tentativa de se chegar à raiz do problema que você acaba totalmente confuso a respeito de qual deles é importante".
"Através do treinamento real", Minoura diz, "você será capaz de descobrir dúzias de problemas e também será capaz de chegar às raízes desses problemas. Você será capaz de fazer inúmeras melhorias. Se você incorporar todo o conhecimento acumulado na busca pela raiz da causa dos problemas durante os vários ‘Por que? Por que? Por que?...’ no seu equipamento, então você terá algo que ninguém mais terá a oportunidade de ter. Eu não creio que isso tenha alguma relação com a nacionalidade; e sim com se você recebeu ou não um treinamento adequado. Eu creio que essa tendência de dar tal tipo de treinamento e educação forme a base para o método da Toyota conhecido como monozukuri".
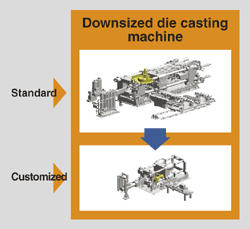 |
Máquina de fabricar moldes de tamanho certo, desenvolvida pela Toyota, customizada para refletir o formato final do produto, custo 50% menos que sua antecessora. (Fonte Toyota Anuual Report 2003) |
Em última instância, o objetivo do TPS é conseguir reduções duradouras de custos. E o princípio básico do TPS não é algo que irá mudar. Mas o mundo continua mudando, e Minoura sugere quatro métodos para poder lidar com isso.
Primeiro, quando considera que fatores permitiram à produção japonesa alcançar supremacia mundial, Minoura ressalta que a alta qualidade foi um dos fatores chave. "Entretanto, nos dias atuais, os fabricantes de carros de outros países e fornecedores de autopeças conseguiram chegar próximo aos níveis de qualidade do Japão. Isso significa que nós temos que pensar muito sobre o que deve ser feito para manter nossa preeminência na área de qualidade".
Segundo, como os negócios automotivos estão se tornando crescentemente globais, Minoura afirma: "É importante mudar nosso foco de sermos centrados no Japão para sermos mais globalizados, algo que também está de acordo com nosso princípio de genchi genbutsu (experiência própria), e pensar exatamente que forma essa mudança deve tomar".
Terceiro, Minoura acha que o futuro será ver um aumento da necessidade de incorporar nos produtos o que o cliente necessita e deseja."É necessário que os fornecedores trabalhem conosco em todos estágios para encontrarmos um jeito de produzir melhor e mais barato. Este tipo de colaboração pode trazer as novas idéias que precisamos".
Por último, Minoura diz que "para permitir que o DNA da Toyota se espalhe e evolua globalmente, precisamos desenvolver e treinar pessoas globalmente".
Mas os esforços para se construir qualidade no processo de produção estão sendo esquecidos, de acordo com Minoura. "Quando falamos sobre os defeitos na nossa fábrica, falamos sobre os processos defeituosos. Se há um processo defeituoso, isso irá resultar em produtos defeituosos. Por mais que você examine minuciosamente um produto defeituoso, você não conseguirá aperfeiçoar o processo. Então devemos olhar para o processo com problema. Os componentes são levados de um fornecedor para outro em um fluxo e ao menos que exista um excelente sistema de controle, é impossível prevenir que os defeitos aconteçam. Estabelecer tal sistema de controle é a coisa mais fácil de se fazer quando a cadeia de abastecimento é simples. E esse é um assunto que a gerência superior deveria ter responsabilidade".
Treine as pessoas para seguir as regras e padrões como se isso fizesse parte da natureza deles
Não obstante, o ser humano é aquele que realmente consegue construir qualidade no produto. Segundo Minoura, "é importante criar um clima no qual as pessoas são treinadas a seguir as regras e padrões como se isso fizesse parte da natureza deles". "Este tipo de resposta reflexiva é um destaque do monozukuri da Toyota".
É essencial criar relacionamentos de confiança mútua. Minoura vê a localização ou genchika como chave para isso. "Quando iniciei meus trabalhos nos EUA, tivemos que manter algumas funções ainda no Japão, mas hoje estamos tentando fazer tudo o que for possível nos EUA. A estratégia chave para isso agora é o genchika pessoal. O sucesso do genchika depende de quão capazes nós podemos ser para que os empregados locais "herdem" o nosso DNA da Toyota".
Descubra onde é fabricada uma peça com baixo preço e use esse preço como benchmark
O objetivo básico é manter o aumento do nível de fornecimento local. "Se nós descobrirmos que existe um lugar no mundo onde pode se produzir esta ou aquela peça por este ou aquele preço, então deveríamos usar aquele preço como benchmark, além de tentar fazer fluir nossos esforços na tentativa de encontrar um jeito mais barato de se fabricar na própria região", segundo Minoura. "Pessoalmente, eu acho que de longe esta é a melhor maneira de atacar esse problema. Se pudermos baratear a produção local, então o incentivo para comprar de outros mercados irá desaparecer. Mas para que isso realmente aconteça, para realmente dizer ‘OK, eles podem fazer isso por tantos dólares, então podemos fazer o mesmo mais barato aqui’, é preciso que haja colaboração entre a indústria automotiva e seus fornecedores. É por essa razão que nós fabricantes temos a responsabilidade de procurar pelo menor preço, e devemos nos esforçar ao máximo para encontrar um meio de se produzir por muito menos no mercado local, até mesmo no Japão".
Minoura adverte que o fornecedor precisa mudar seu foco para o usuário do carro ao invés do fabricante do carro. "Você terá que começar a analisar as necessidades e preferências do usuário final. Você deverá descobrir o que o usuário final deseja e deverá trabalhar para desenvolver componentes que se ajustem a essas necessidades. Então você estará oferecendo o que você realmente desenvolveu para fabricantes de carros como nós, que irão incorporar estes componentes aos nossos projetos. Esse é o próximo perfil de produção que a indústria vem buscando. Quando isso acontece, têrmos como "fabricantes de carro" e "fornecedores" se tornarão inapropriados. Esses dois irão se aproximar, tornando-se parceiros, e juntos desenvolverão alta qualidade, preços menores e produtos que atendam às necessidades do usuário final. Para sobreviver, será preciso usar o conhecimento que você adquiriu no chão de fábrica para reduzir os custos e utilizar esse dinheiro economizado no desenvolvimento. Você precisa fazer um esforço extra para permitir a você enxergar a sua próprias forças e compará-las com as dos seus concorrentes".
Desenvolva as pessoas para poderem ter idéias interessantes
Minoura não pode enfatizar demasiadamente o papel da liderança que as pessoas têm no monozukuri. "Não pode haver nenhum bem sucedido monozukuri (fazer produtos) sem hitozukuri (fazer pessoas). Para manter o surgimento de novas técnicas revolucionárias de produção, precisamos desenvolver idéias e conhecimentos singulares através do pensar nos problemas nos termos do genchi genbutsu. Isso significa que há necessidade de se pensar sobre como podemos desenvolver pessoas que possam gerar estas idéias. Na medida em que nossas operações se tornam cada vez mais globalizadas, também há a necessidade de se pensar em como introduzir o DNA da Toyota nos funcionários de todas regiões do mundo".
A Toyota exporta mundialmente seu enfoque singular sob o rótulo de "Toyota Way". Como parte deste esforço, o Toyota Institute foi fundado no Japão em Janeiro de 2002 para educar gerentes e executivos tanto do Japão como de outros países. "Cada ano", Minoura ressalta, "dezenas de funcionários de todas nossas afiliadas ao redor do mundo desembarcam no Japão para aprender o Toyota Way".